Indholdsfortegnelse:
- Trin 1: Materialeliste og -proces
- Trin 2: Fremstilling af magnetpladerne
- Trin 3: Oprettelse af Stator
- Trin 4: Test og sensorer
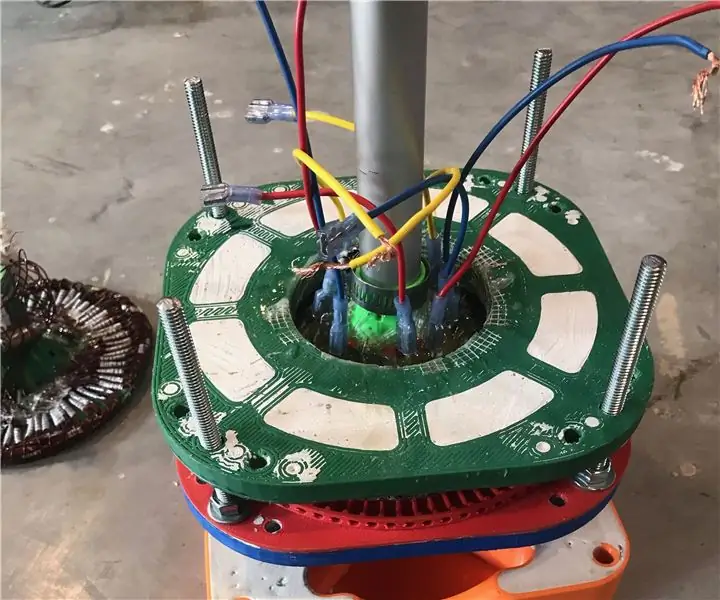
Video: 3D -printet Axial Flux -generator og dynamometer: 4 trin (med billeder)
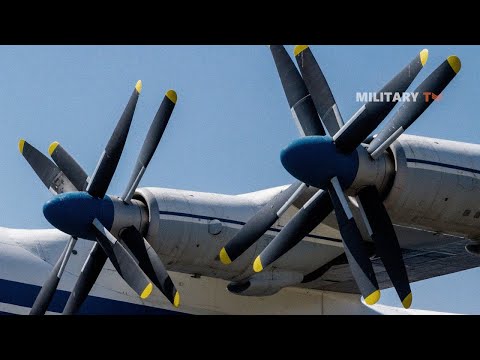
2024 Forfatter: John Day | [email protected]. Sidst ændret: 2024-01-30 08:28
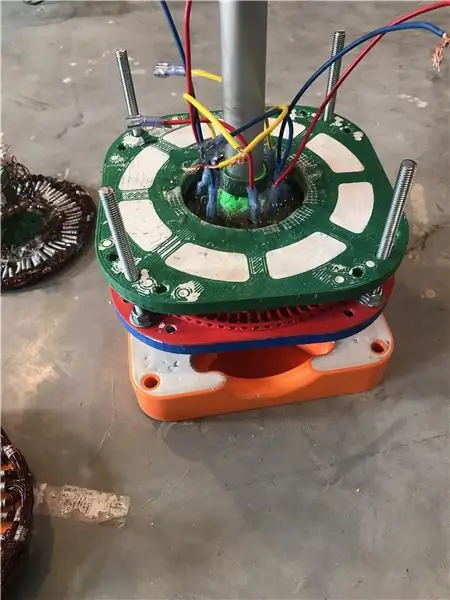
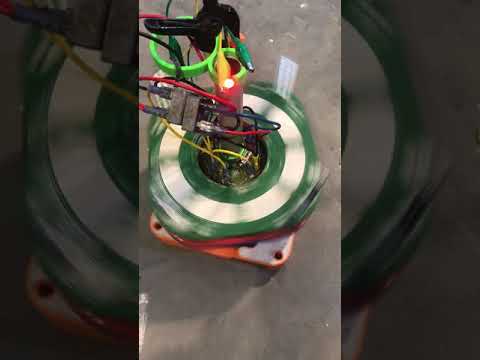
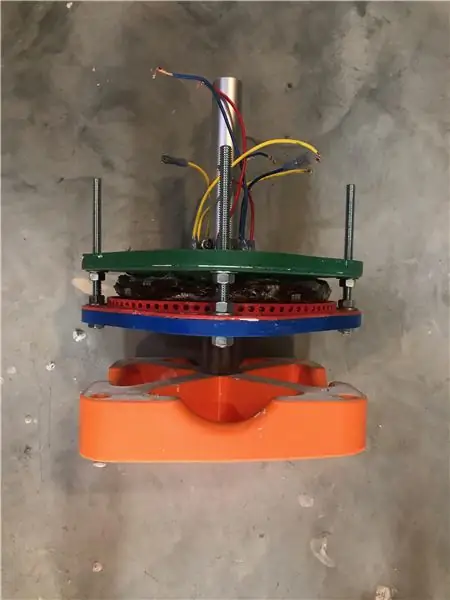
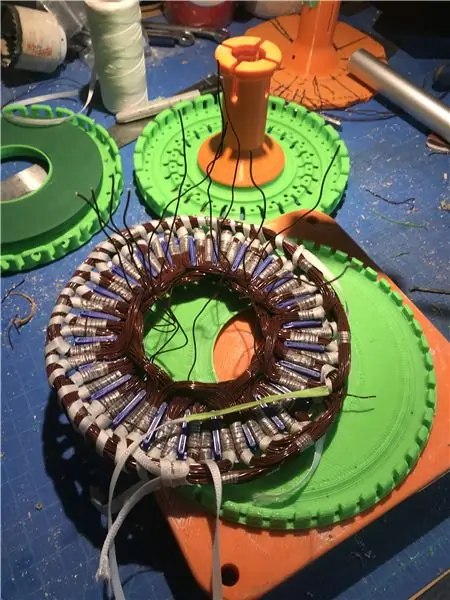
HOLD OP!! LÆS DETTE FØRST !!! Dette er en oversigt over et projekt, der stadig er under udvikling. Du er velkommen til at tilbyde support.
Mit endelige mål er, at denne type motor/generator kan blive et parametriseret open source -design. En bruger skal kunne indtaste nogle parametre, f.eks. Drejningsmoment, hastighed, strøm, volt/omdrejninger pr. Minut, almindelige magnetstørrelser og måske ledig plads, og der skal genereres en række 3D -udskrivbare.stl- og.dxf -udskårne filer.
Det, jeg har gjort, er skabt en platform, der kan validere et simuleret design, som derefter kan udvikles til en mere optimal enhed efter fællesskab.
Dels er dette en af grundene til, at jeg har konfigureret dette med et dynamometer. Et dynamometer måler drejningsmoment og hastighed for at tillade hk eller aksel Watt at måle. I dette tilfælde har jeg bygget generatoren med en gennemgående, stationær aksel, hvilket gør opsætningen af et dynamometersystem enklere, og så den kan konfigureres til at blive drevet som en motor af en RC ESC (håber jeg), og drejningsmoment måles på output, samt hastighed, V og ampere, så motoreffektivitet kan bestemmes.
Til mine formål kan den drives af en motor med variabel hastighed (overskud fra akku -boremaskine, med trinvis gearing), og akselmomentindgang måles, samt V og forstærkere ud, så der kan genereres reel effektivitet og de forventede turbinebelastninger der skal simuleres.
I denne tilstand håber jeg at bruge en RC ESC, der er i stand til regenerativ bremsning, og måske en Arduino til at styre den belastning, min VAWT bærer for at opnå MPPT (Multi Power Point Tracking).
MPPT bruges i både sol- og vindmøllestyring, men det er lidt anderledes for vind. Med vindkraft er et stort problem, at efterhånden som vindhastigheden fordobles 10 km/t til 20 km/t, stiger energien fra vinden med terningen, så med 8 gange. Hvis 10W var tilgængelig ved 10 km/t, så er 80W tilgængelig ved 20 km/t. Det er dejligt at have mere energi, men generatorer output fordobles kun som hastighed fordobles. Så hvis du har den perfekte generator til en vind på 20 km/t, kan dens belastning være så stærk, at den ikke engang starter ved 10 km/t.
Hvad MPPT gør, er at bruge en kraftig solid state -switch til at afbryde og derefter tilslutte en generator igen meget hurtigt. Det giver dig mulighed for at justere, hvor meget belastning en generator bærer, og Multi, af MPPT, betyder, at du kan indstille forskellige belastninger til forskellige hastigheder.
Dette er meget nyttigt, da alle typer møller samler deres maksimale energi, når belastningen matches med den tilgængelige energi eller vindhastighed.
SÅ
Dette er ikke en opskrift, selvom jeg tror, at den kunne kopieres fra det, jeg har sendt, og jeg vil med glæde levere yderligere oplysninger, men jeg foreslår, at den bedste løsning ville være at foreslå forbedringer til mig, inden kredsløb og sensorer -konkurrencen slutter, så jeg kan overveje, svare og måske forbedre dette instruerbare.
Jeg vil fortsætte med at opdatere, revidere og tilføje oplysninger, så hvis det er interessant nu, vil du måske tjekke ind igen om lidt, men jeg håber at få gjort en hel del, før Sensors -konkurrencen slutter den 29/19 juli.
Jeg er heller ikke et særligt socialt dyr, men jeg kan godt lide et klap på skulderen nu og da, og det er en af grundene til, at jeg er her:-) Fortæl mig, hvis du nyder at se mit arbejde, og vil se mere, tak:-)
Dette projekt opstod, fordi jeg ønskede en kontrollerbar belastning til test af mine mølledesign, og jeg ville have, at det var let at reproducere, så andre også kunne bruge det. Til dette formål begrænsede jeg mig til at designe noget, der kun kunne bygges med en FDM -printer, og der var ikke brug for andre værktøjsmaskiner. Der ser ikke ud til at være mange kommercielle produkter, der opfylder behovet for et højt drejningsmoment, lav hastighed, ikke -tandhjulsgenerator, selvom der er et par stykker fra Kina. Generelt er der ikke meget efterspørgsel, fordi gearsystemer er så billige og elektricitet er så billig.
Det, jeg ønskede, var noget, der producerede omkring 12V ved 40-120 omdr./min. Og omkring 600-750W ved 120-200rpm. Jeg ville også have, at den var kompatibel med billige 3 -fasede PMA -controllere fra RC -verdenen (ESC's Electronic Speed Controllers). Et sidste krav var, at det var en udløber (kasse eller skal med magneter roterer, mens aksel med stator er stationær), med en aksel, der passerer hele vejen igennem sagen, og en stator, der klemmer til akslen.
Dette instruerbare er et igangværende arbejde, og jeg lægger det op, så folk kan få et overblik over processen, ikke så meget, fordi jeg synes, de skal kopiere det. En vigtig ting, jeg ville ændre, er, at wirestøttepladen, jeg byggede, ikke er nær stærk nok til korrekt at kanalisere magnetfelterne rundt om ringen, så en stor del af den magnetiske flux, der er betalt for i disse magneter, er spildt på bagsiden. Når jeg lavede designet om, hvilket jeg snart skal lave, ville jeg sandsynligvis gøre det med de magnetiske bagplader som cnc -skårne stålplader. Stål ville være rimeligt billigt, meget stærkere og ville forenkle det meste af denne konstruktion. Det var interessant at lave FDM/wire/gips -kompositterne, som jeg har illustreret her, og med jernbelastet PLA ville tingene også have været anderledes. Jeg besluttede dog, at jeg ville have noget, der virkelig ville vare, så stålplader.
Jeg har gjort gode fremskridt med denne version, som jeg vil bruge til at teste denne VAWT. Jeg er ikke helt der med hensyn til lavspændingsydelse endnu. Jeg tror, min Wattage/Torque er i den rigtige boldbane, jeg opdaterer, efterhånden som tingene skrider frem, men på dette tidspunkt har det, jeg har, en god chance for at være den kontrollerbare belastning, jeg har brug for. Når den er kortsluttet, ser det ud til at kunne levere en del momentmodstand, mere end nok til at teste møllen. Jeg skal bare oprette en kontrolleret modstandsbank, og jeg har en ven, der hjælper mig med det.
En ting, jeg kort vil behandle, er, at jeg som mange mennesker nu har haft en 3D (FDM-brugende PLA) printer i et par år, som jeg har haft 20-30 kg glæde af. Jeg synes ofte, det er frustrerende, da dele af enhver størrelse/styrke enten er dyre og meget langsomme at udskrive, eller billige, hurtige og spinkle.
Jeg ved, hvor mange tusinder af disse 3D -printere der er, der ofte ikke gør noget, fordi det tager for lang tid eller koster for meget at lave nyttige dele. Jeg er kommet med en interessant løsning til stærkere hurtigere dele fra den samme printer og PLA.
Jeg kalder det en "hældt struktur", hvor det trykte objekt (bestående af 1 eller flere trykte dele, og nogle gange lejer og aksler), er lavet med hulrum, der er designet til at blive hældt fuld af et hærdende flydende fyldstof. Nogle af de oplagte valg for en hældt fyld ville naturligvis være noget i stil med epoxy fyldt med kortstrenget hakket glasfiber, som kunne bruges til højstyrke og letvægtssamlinger. Jeg prøver også nogle lavere omkostninger, mere miljøvenlige ideer. Den anden side af denne "hældte struktur" -samling er, at det hulrum eller hulrum, du skal fylde, kan have elementer med høj trækstyrke med lille diameter, spændt forspændt på den trykte "form/prop", hvilket gør den resulterende struktur en komposit i materialer og i struktur, del Stressed Skin (PLA -kappen), men med en høj komprimeret stregth -kerne, der også indeholder elementer med høj trækstyrke. Jeg vil lave en anden instruerbar med dette, så vil tale om det her, kun for at dække, hvordan det vedrører denne build.
Trin 1: Materialeliste og -proces
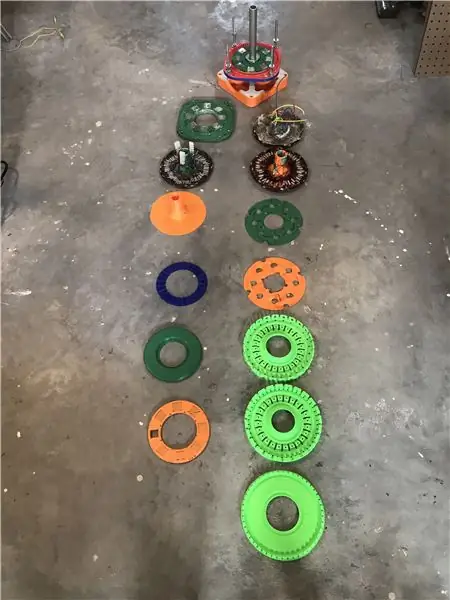
PMA består af 3 samlinger, hver samling indeholder eller bruger en række dele og materialer.
Fra top (lejeside) til bund (statorside), 1. Bærebærer og toplejeray
2. Stator
3. Nedre magnetrække
1. lejebæreren og topmagneten
Til dette brugte jeg 3D -printede dele, der er anført ovenfor
- 150mm8pol øvre mag og lejestøtte CV5.stl,
- lejeside indvendig plade
- lejesiden ydre plade
- 1 "ID selvjusterende leje (som brugt i standard pudeblokke ++ tilføj internetlink),
- 25 'af 24g galvaniseret ståltråd
- 15 'af 10g galvaniseret ståltråd
- 2 ruller groft ståluld
Eventuelt kan den tunge ståltråd og ståluld erstattes med stålplader, laser / vandstrålesnit eller en 3D -printet magnetisk bagplade kan være mulig (men tung noget ståltråd er stadig en god idé, da det vil modstå plastisk deformation over tid). Jeg har prøvet at støbe en bagplade med epoxy fyldt med jernoxidpulver og havde en vis succes. Forbedring af fluxkoblingen mellem magneter i arrayet lateralt ved hjælp af en mere effektiv bagplade bør øge volt ud ved lavere omdrejninger. Det er også godt at huske på, at dette er den væsentligste strukturelle komponent, og bagpladen overfører kræfterne fra magneterne til jack -stolperne. De magnetiske kræfter, der trækker pladerne mod hinanden, kan være hundredvis af lbs, og kræfterne stiger eksponentielt (Cubed, til den tredje effekt), når pladerne kommer tæt sammen. Dette kan være meget farligt, og der skal udvises forsigtighed med værktøjer og andre genstande, der kan blive tiltrukket af den samlede plade, eller hvis den er tilbage!
Jeg brugte omkring 300 fod 24g belagt magnettråd i viklingerne, som jeg senere vil dække detaljeret.
Trin 2: Fremstilling af magnetpladerne
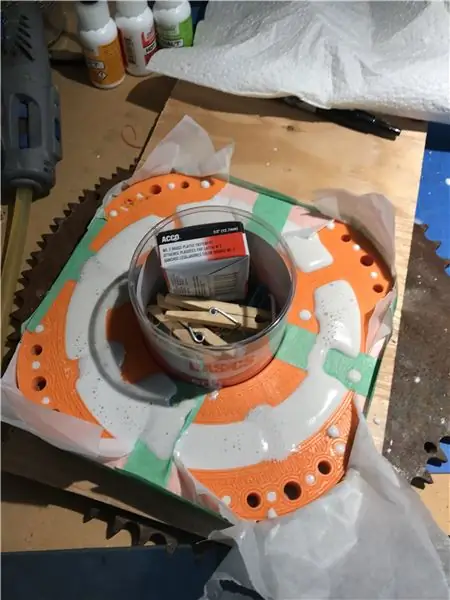
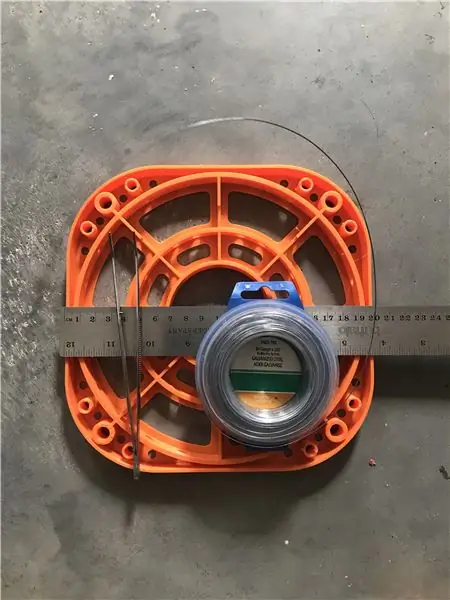
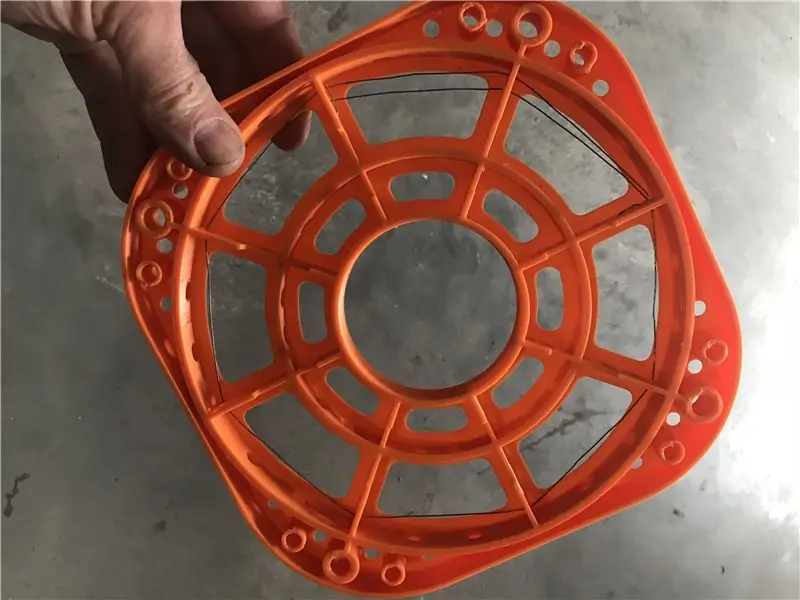
I denne aksiale fluxgenerator bruger jeg to magnetarrays, en på hver side af statorspolerne, for at minimere tandhjul og maksimere output. Det betyder, at der ikke er behov for en magnetisk kerne for at trække magnetfeltet gennem kobberviklingerne, som de fleste motor/alt geometrier gør. Der er nogle aksiale fluxdesigner, der bruger pariserkerner, og jeg kan prøve nogle eksperimenter på den måde i fremtiden. Jeg vil gerne prøve noget 3d -trykbart jernbelastet materiale.
I dette tilfælde har jeg valgt et 8 -polet magnet array i omkring en 150 mm cirkel ved hjælp af 1 "x1" x0.25 "sjældne jordartsmagneter. Denne størrelse skulle sikre, at alle dele ville passe på en 210 mm x 210 mm print seng. Generelt har jeg først dimensioneret denne generator ved at forstå, at jo større diameter, jo bedre målt i volt pr. Omdrejninger pr. magneter, jo længere magneterne er fra midten, jo hurtigere rejser de, og der er også mere plads til kobber! Alle disse ting kan tilføje hurtigt! Men en konklusion, jeg er kommet til, er, at i dette størrelsesinterval er en konventionel flux system kan være en bedre hjemmebygning. Små rotorer har ikke meget plads, og tingene kan blive ret stramme, især hvis du laver en gennemgående aksel som jeg har gjort i dette design. Også hvis din magnet (radial længde) er lille i forhold til din rotordiameter, som i denne, (omtrent 6 "diameter til 1" magnet), så vind ng bliver lidt mærkelig, idet den indvendige endevikling kun er omkring 1/2 længden af den ydre.
Tilbage til instruktionen! Den måde, jeg har samlet magnetpladerne på denne generator på, er først at lime magnetpladen (grøn) til den røde flange/bagplade. Jeg lagde derefter magnetpladen på et par tynde lag krydsfiner (ca. bag på magnetpladerne. Dette gik ikke helt som jeg havde håbet. Det stærke magnetfelt trak ledningen mod midten af magneterne, og det lykkedes mig ikke at bøje hver række af tråd for at passe perfekt til det næste sted, uden at skubbe den første pakning. Jeg havde håbet, at jeg bare kunne spole tråden ind, og den magnetiske strømning ville låse den ned. Derefter forsøgte jeg at skære trådringe, og dette var bedre, men stadig langt fra, hvad jeg ville håbede med hensyn til at få en flot konsekvent bagplade fra tråd. Mere komplekse måder at få dette gjort på er mulige og kan være værd at eksperimentere i fremtiden. Jeg forsøgte også at bruge ståluld, komprimeret i magnetfeltet, som en bagplade eller flux Dette syntes at virke, men den faktiske jerntæthed syntes ikke at være særlig høj, så jeg di testede ikke dens effektivitet, dels fordi jeg troede, at trådstrukturen var vigtig for de mekaniske belastninger på magnetpladerne. Stålulden kan også være en fremtidig undersøgelse værd, men vandstråleskårne stålplader er sandsynligvis den næste mulighed, jeg vil prøve.
Derefter tog jeg den orange 3D -udskrevne del og vævede tråd gennem og omkring den langs det, der forekom mig at være retninger for højeste belastning, bolt til bolt og bolt til at centrere et par gange på hvert hjørne. Jeg viklede det også rundt om bolthullerne, hvor hele trådstangen passerer som jekkestolper for at holde og justere afstanden mellem pladerne.
Efter at have været tilfreds med, at magnetpladen og flangen var gode nok, og den orange bagplade var tilfredsstillende gevind med forstærkningstråd, sluttede jeg de to med lim. Der skal udvises forsigtighed, da denne limfuge skal være vandtæt eller lukke. Jeg havde lækager de to første gange, og det er rodet, spilder meget puds og er mere stress end du har brug for. Jeg vil anbefale at holde noget blåklæb eller anden tyggegummi som ikke permanent klæbemiddel rundt for at lappe lækager hurtigt. Når delene er forbundet, skal du fylde det forstærkede materiale efter eget valg. Jeg brugte et hårdt gips, modificeret med PVA -lim. Gipset formodes at nå 10.000 psi komprimerende, men ikke meget i spænding (dermed tråden). Jeg vil gerne prøve epoxy med hakket glas og cabosil eller beton og tilsætningsstoffer.
En praktisk ting ved gipset er, at når det sparker, har du en hel del tid, hvor det er svært, men skrøbeligt og utætheder eller klatter let kan skrabes eller bankes af.
I dette design er der to magnetplader. Den ene har et leje, en standard 1 pudeblok selvjusterende enhed. Jeg pressede min tidligt ind i magnetarrayet. Til den applikation, jeg har designet den til, vil et andet leje være placeret i turbinen over generatoren, så jeg brugte kun det ene selvjusterende leje. Dette var lidt af en smerte i sidste ende. Disse dele kunne også samles med hver magnetplade med et leje, hvis udgangstrådene fra statoren blev ført internt gennem den monterede aksel. Dette ville tillade kontra roterende drivmaskiner at blive monteret på en fælles, ikke -roterende aksel/rør.
Trin 3: Oprettelse af Stator

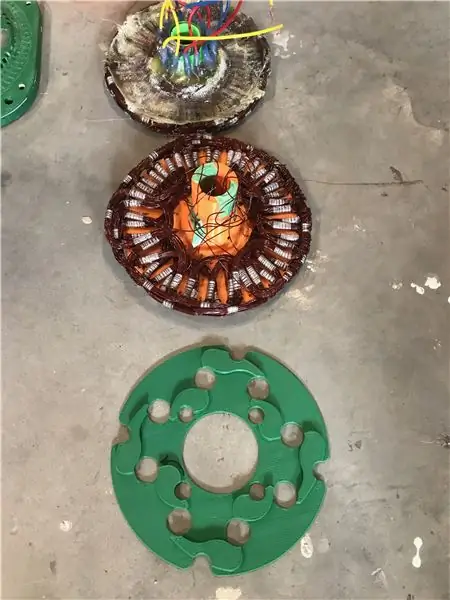
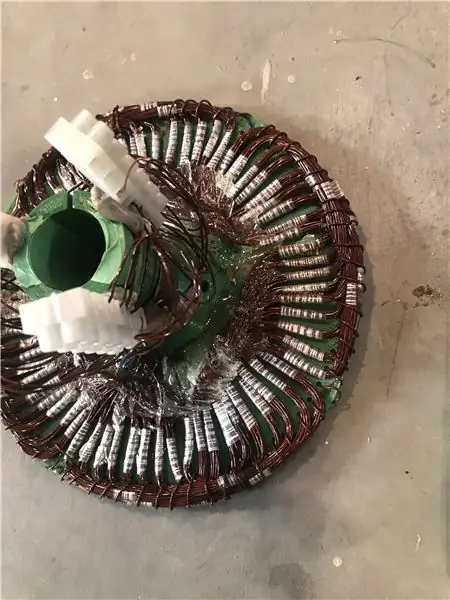
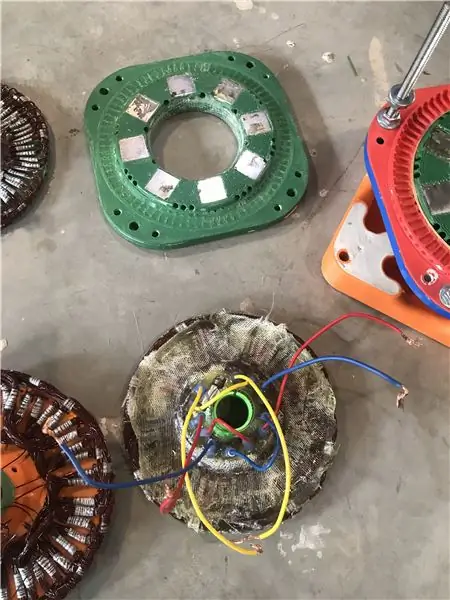
I tråd med mit tema om at forsøge at forklare, hvad jeg har gjort, og hvorfor det på det tidspunkt virkede som en god idé, vil statoren kræve lidt mere plads.
I en PMA er viklingerne generelt stationære, mens de magnetiske samlinger roterer. Dette er ikke altid tilfældet, men næsten altid. I en aksial fluxenhed, med forståelsen af den grundlæggende "højre håndsregel", forstås det, at enhver leder, der støder på et roterende magnetfelt, vil have strøm og spænding genereret mellem trådens ender, idet mængden af nyttig strøm er proportional til feltets retning. Hvis feltet bevæger sig parallelt med tråden (f.eks. I en cirkel omkring rotationsaksen), vil der ikke blive genereret nogen nyttig strøm, men der vil blive genereret betydelige hvirvelstrømme, der modstår magneternes bevægelse. Hvis tråden kører vinkelret, nås den højeste spænding og strømudgang.
En anden generalisering er, at rummet i statoren, gennem hvilken den magnetiske flux passerer, mens den er i rotation, for maksimal watteffekt, skal fyldes med så meget kobber, alt radialt lagt, som muligt. Dette er et problem for aksiale fluxsystemer med lille diameter, da det område, der er tilgængeligt for kobber nær akslen, i denne sag er en brøkdel af området ved yderkanten. Det er muligt at få 100% kobber i det indre mest område, som magnetfeltet støder på, men inden for denne geometri får du kun 50% på yderkanten. Dette er en af de stærkeste grunde til at holde sig væk fra aksiale fluxdesign, der er for små.
Som jeg tidligere har sagt, handler denne instruktive ikke om, hvordan jeg ville gøre det igen, mere det er at pege i nogle retninger, der virker lovende, og vise nogle af de huller, der kan nås på denne vej.
Ved udformningen af statoren ville jeg gøre den så fleksibel som muligt med hensyn til voltudgang pr. Omdr./min., Og jeg ville have, at den var 3 -faset. For maksimal effektivitet, ved at minimere genererede hvirvelstrømme, bør ethvert "ben" (hver side af en spole betragtes som et "ben") kun støde på en magnet ad gangen. Hvis magneter er tæt på hinanden eller rører som tilfældet er i mange rc -motorer med høj output, vil der i løbet af den tid, "benet" passerer gennem den magnetiske flux -vending, blive udviklet betydelige hvirvelstrømme. I motorapplikationer betyder det ikke så meget, da spolen får strøm fra controlleren, når den er på de rigtige steder.
Jeg dimensionerede magnetarrayet med disse begreber i tankerne. De otte magneter i arrayet er hver 1 "på tværs, og mellemrummet mellem dem er 1/2". Det betyder, at et magnetisk segment er 1,5 "langt, og det har plads til 3 x 1/2" "ben". Hvert "ben" er en fase, så på et hvilket som helst tidspunkt ser det ene ben neutral flux, mens de to andre ser accending flux og faldende flux. Perfekt 3 -faset output, men ved at give neutralpunktet så meget plads (for at minimere hvirvelstrømme) og ved hjælp af firkantede (eller tærteformede) magneter topper fluxen næsten tidligt, forbliver høj og falder derefter hurtigt til nul. Denne type output kaldes jeg trapezformet og kan være vanskelig for nogle controllere, jeg forstår. 1 "runde magneter i det samme apparat ville give mere af en sand sinusbølge.
Generelt er disse hjemmebyggede generatorer blevet bygget ved hjælp af "spoler", doughnutformede bundter af tråd, hvor hver side af doughnut er et "ben", og antallet af spoler kan sættes sammen, i serie eller parallelt. Donuts er arrangeret i en cirkel, med deres centre på linje med midten af magnetbanen. Dette virker, men der er nogle problemer. Et problem er, at da lederne ikke er radiale, passerer en stor del af lederen ikke ved 90 grader til magnetfeltet, så der genereres hvirvelstrømme, der fremstår som varme i spolen og modstand mod rotation i magnetarrayets. Et andet problem er, at fordi lederne ikke er radiale, pakker de ikke så godt sammen. Output er direkte proportional med mængden af tråd, du kan passe i dette rum, så output reduceres med ikke -radiale "ben". Selvom det ville være muligt og undertiden gøres i kommercielle designs, kræver det at opvikle en spole med radiale "ben, forbundet oven og bund, 2x så meget endevikling som en serpentinvikling, hvor toppen af et ben er forbundet til toppen af næste passende ben, og derefter bunden af det ben er forbundet med det næste passende ben, og om og om igen.
Den anden store faktor i Axial flux -generatorer af denne type (roterende magneter over og under stator) er mellemrum mellem pladerne. Dette er et kubelovsforhold, da du reducerer afstanden mellem plader med 1/2, stiger magnetisk fluxdensitet med 8x. Jo tyndere du kan gøre din stator, jo bedre!
Med dette i tankerne lavede jeg en 4 -flettet snoede jig, oprettede et system til måling af omkring 50 fod trådtråde og pakkede jiggen 6 gange og skabte trådbundter med en diameter på ca. 6 mm. Disse passer jeg på den blå afstandsring, og binder dem ned gennem hullerne, så trådenderne kom ud på bagsiden. Det var ikke let. Det blev hjulpet lidt ved at have omhyggeligt tapet bundterne, så de ikke var løse, og ved at tage mig tid og bruge et glat træformningsværktøj til at skubbe ledninger på plads. Når de alle var bundet på plads, blev den blå afstandsring placeret i den største af de lysegrønne baljer, og ved hjælp af det mørkegrønne doughnutformningsværktøj på den anden side af det lysegrønne kar blev den forsigtigt presset fladt med en bænk. Dette formbadekar har en rille, hvor snoretrådene kan sidde i. Dette tager tid og tålmodighed, mens du forsigtigt roterer omkring 1/5 omgang, trykker, roterer og fortsætter. Dette danner disken flad og tynd, samtidig med at endeviklingerne kan stables. Du vil måske bemærke, at min 4 -lobede vikling har lige "ben", men de indre og ydre forbindelser er ikke runde. Dette skulle gøre det lettere for dem at stable. Det fungerede ikke så godt. Hvis jeg gjorde det igen, ville jeg få den indvendige og udvendige endevikling til at følge cirkulære stier.
Efter at have fået det fladt og tyndt og kanterne pakket ned, viklede jeg et fladt bånd rundt om kanten for at komprimere det, og et andet op, ned og omkring hvert ben og derefter til det ved siden af det også. Når dette er gjort, kan du fjerne slipsetrådene og skifte til det mindre pressekar og gå tilbage til skruestikken og trykke den så tynd og flad som muligt. Når det er fladt, fjern det derefter fra pressekarret. I stedet for den komplekse proces med omhyggelig voksbehandling og belægning af forme som denne med frigivelsesforbindelser, bruger jeg generelt bare et par lag strækfolie (fra køkkenet). Læg et par lag i bunden af formen og læg glasfiber på strækfolien. Tilføj derefter statormonteringsrøret, der passer til toppen af det lysegrønne formbadekar, men har laget af stretchfolie og glasfiber imellem. Tilføj derefter statorviklingen tilbage på plads for at skubbe både stretchfolien og glasfiber ned og låse stators monteringsrør på plads. Vend derefter tilbage til skruestikken og tryk fladt igen. Når det passer godt ind i karret, med stretchfolien og glasfiber klemt i, tilføjes glasfiberdug (med et hul i midten til statormonteringsrøret).
Nu er det klar til at hælde bindematerialet, epoxy eller polyesterharpiks bruges ofte. Inden dette er udført, er omhyggelig forberedelse vigtig, da når du først har startet denne proces, kan du ikke rigtig stoppe. Jeg brugte en 3D -printet bundplade, jeg tidligere havde lavet, med et 1 "hul i midten og en flad plade omkring det. Jeg brugte et 16" stykke 1 "aluminiumsrør, som statormonteringsrøret ville passe over og være holdt vinkelret på den flade plade. Det grønne formbadekar, statorviklingen og statormonteringsrøret blev skubbet ned for at sidde på den flade plade. Før jeg blandede epoxy, læste jeg først 4 stykker krympepapir og lagde forsigtigt et 5. stykke på mørkegrønne dannende doughnut, så den ville have de mindste rynker i ansigtet mod statorviklingen. Efter at have blandet epoxyen og hældt den på glasfiberkluden, lagde jeg forsigtigt strækfolien rundt om 1 "røret og lagde den grønne danner ring oven på den. Jeg havde også forberedt et par gamle bremserotorer, som gav en vis vægt, og sad pænt på den grønne formende doughnut. Efter dette lagde jeg en omvendt gryde oven på bremserotorerne, og oven på gryden stablede jeg omkring 100 lbs ting. Jeg forlod dette i 12 timer, og det kom ud omkring 4-6 mm tykt.
Trin 4: Test og sensorer
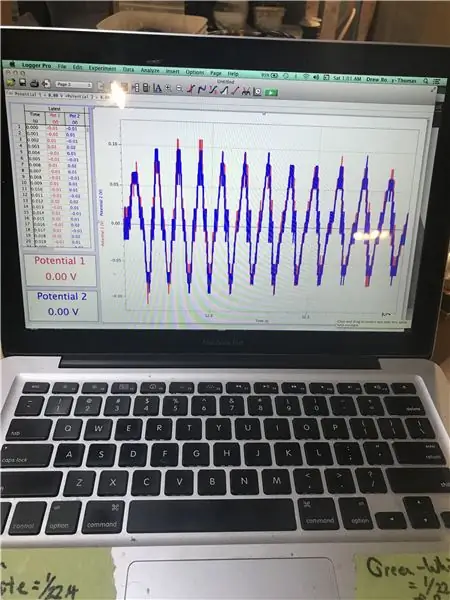
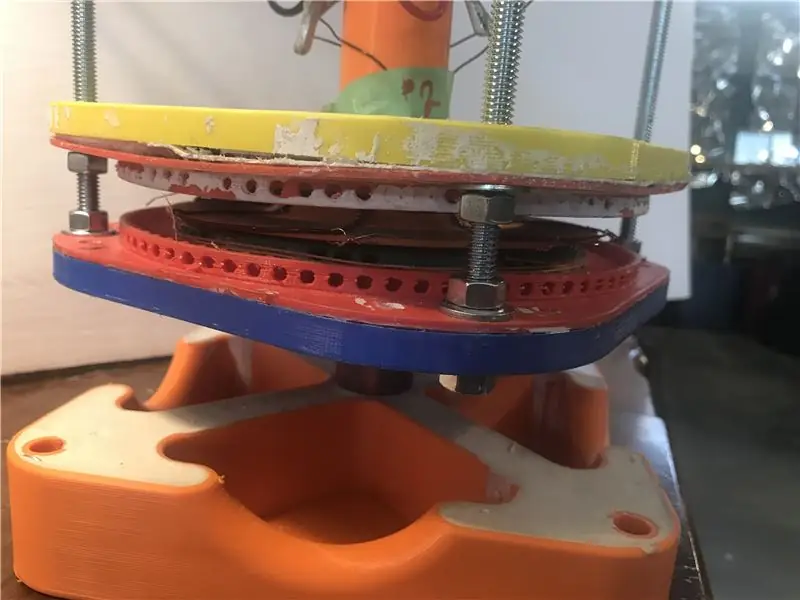
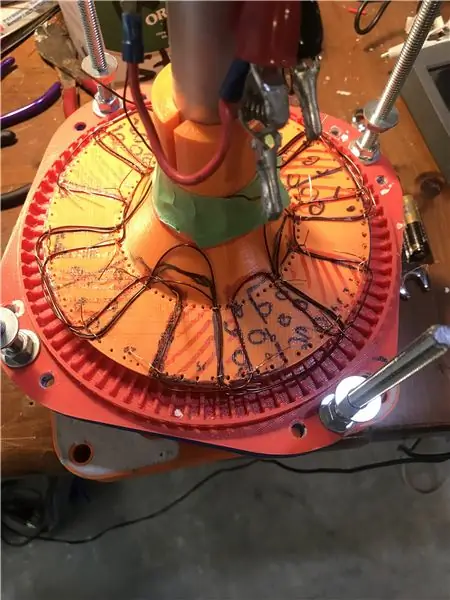
Der er en række målbare input og output fra generatoren, og måling af dem alle, på samme tid er ikke let. Jeg er meget heldig at have nogle værktøjer fra Vernier, der gør det meget lettere. Vernier laver produkter på uddannelsesniveau, ikke certificeret til industriel brug, men meget nyttige for eksperimenter som mig selv. Jeg bruger en Vernier datalogger med en række plug and play sensorer. På dette projekt bruger jeg hallbaserede strøm- og spændingsprober til at måle generatorens output, en optisk sensor til at give generatorens hastighed og en vejecelle til at måle momentindgang. Alle disse instrumenter samples cirka 1000 gange i sekundet og optages på min bærbare computer ved hjælp af Vernier -loggeren som en AD -gennemføringsenhed. På min bærbare computer kan den tilhørende software køre realtidsberegninger baseret på input, der kombinerer drejningsmoment- og hastighedsdata for at give realtid input -akseleffekt i watt og real -time outputdata i elektriske watt. Jeg er ikke færdig med denne test, og input fra en person, der har en bedre forståelse, ville være nyttig.
Et problem, jeg har, er, at denne generator virkelig er et sideprojekt, og derfor vil jeg ikke bruge for meget mere tid på det. Som det er, tror jeg, at jeg kan bruge det til en kontrollerbar belastning til min VAWT -forskning, men til sidst vil jeg gerne arbejde med mennesker for at forfine det, så det er et effektivt match til min turbine.
Da jeg begyndte på VAWT -forskning for omkring 15 år siden, indså jeg, at testning af VAWT's og andre prime movers er mere kompleks, end de fleste mennesker er klar over.
Et primært problem er, at energien repræsenteret i en væske i bevægelse er eksponentiel for dens bevægelseshastighed. Det betyder, at når du fordobler hastigheden af et flow, stiger energien i strømmen 8x (det er i terninger). Dette er et problem, da generatorer er mere lineære og generelt, hvis du fordobler omdrejningstallet for en generator, får du omkring 2x watt.
Denne grundlæggende uoverensstemmelse mellem møllen (energiopsamlingsenhed) og generatoren (akseleffekt til nyttig elektrisk strøm) gør det svært at vælge en generator til en vindmølle. Hvis du vælger en generator-match til din vindmølle, der vil generere den mest tilgængelige strøm fra 20 km/t vind, vil den sandsynligvis ikke engang begynde at dreje før 20-25 km/t, da belastningen på møllen fra generatoren vil være for høj. Med denne generator match, når vinden er over 20 km, vil ikke kun møllen fange en brøkdel af den energi, der er tilgængelig i vinden med højere hastighed, kan møllen overspille og blive beskadiget, da belastningen fra generatoren ikke er høj nok.
I det sidste årti er en løsning blevet mere økonomisk på grund af prisfaldet på kontrolelektronik. I stedet for at forsøge at matche en række hastigheder beregner designeren den maksimale hastighed, som enheden er beregnet til at køre med, og vælger en generator baseret på mængden af energi og ideel hastighed for møllen ved den hastighed eller lidt over. Denne generator, hvis den er forbundet til dens belastning, vil normalt give for meget drejningsmoment ved lavt hastighedsområde, og den overbelastede turbine vil ikke fange al den energi, den kunne have, hvis den var korrekt belastet. For at oprette den korrekte belastning tilføjes en controller, der kortvarigt afbryder generatoren fra den elektriske belastning, så turbinen kan køre hurtigere til den korrekte hastighed, og generatoren og belastningen tilsluttes igen. Dette kaldes MPPT (Multi Power Point Tracking). Regulatoren er programmeret således, at når turbinehastigheden ændres (eller generatorens spænding stiger), tilsluttes eller afbrydes generatoren, tusind gange i sekundet eller deromkring, for at matche den belastning, der er programmeret til den pågældende hastighed eller spænding.
Anbefalede:
Three Axial Tow Truck (cnc) - PLC: 4 trin
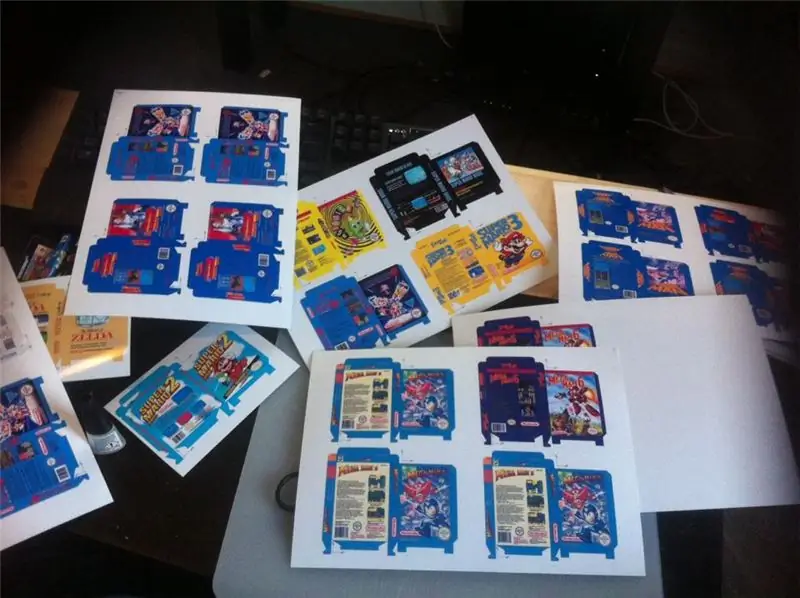
Three Axial Tow Truck (cnc)-PLC: Hej Den foreliggende afhandling omhandler programmering af PLC-PS3 af KLOKNER MOELLER, med begge formål funktionaliteten af en mekanisk model, den såkaldte tre-aksede transportkran og i vores tilfælde transport af metalbelastninger. Det er ess
Brug af Flux - Grundlæggende for lodning: 5 trin
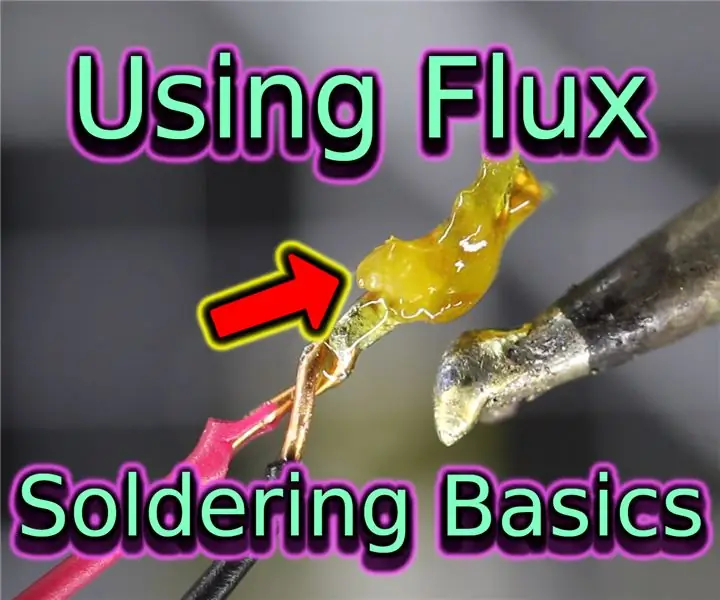
Brug af Flux | Grundlæggende for lodning: Når du lodder, skal loddetagningen knytte et godt bånd til de dele, du lodder på. Metallerne i delene og metallet i loddetøjet skal komme i direkte kontakt med hinanden for at skabe en god binding. Men siden mig
DSUB-15 til USB-adapter til Cobalt Flux DDR-pads: 5 trin
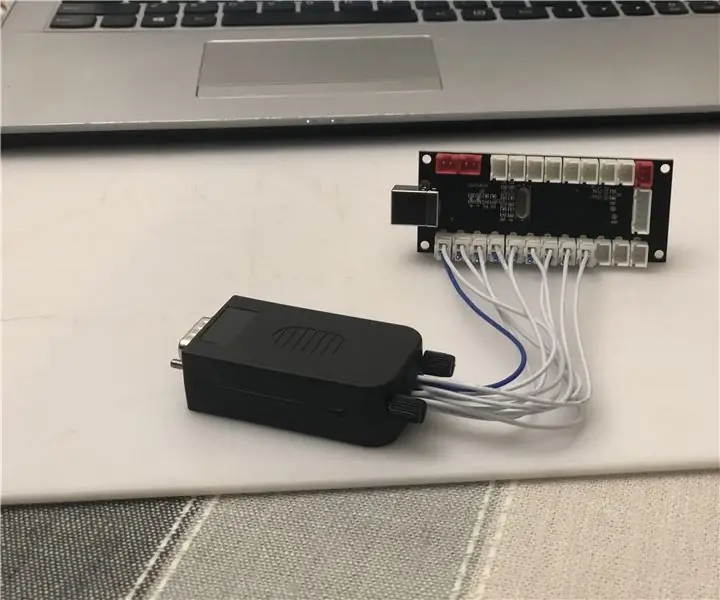
DSUB-15 til USB-adapter til Cobalt Flux DDR Pads: Jeg kom for nylig meget ind i DDR i arkaderne og ville have en egen pad til at spille med Stepmania derhjemme. Efter at have købt en billig måtte på Amazon og ikke været helt tilfreds, fandt jeg en Cobalt Flux DDR -pude på mit lokale OfferUp. Det kom dog ikke med
Sådan adskilles en computer med nemme trin og billeder: 13 trin (med billeder)
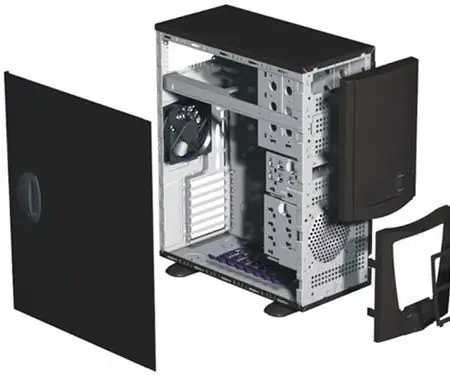
Sådan adskilles en computer med nemme trin og billeder: Dette er en instruktion om, hvordan du adskiller en pc. De fleste af de grundlæggende komponenter er modulopbyggede og nemme at fjerne. Det er dog vigtigt, at du er organiseret omkring det. Dette hjælper med at forhindre dig i at miste dele og også ved at lave genmonteringen til
Sådan styrer du husholdningsapparater med fjernsyn med fjernbetjening med timerfunktion: 7 trin (med billeder)
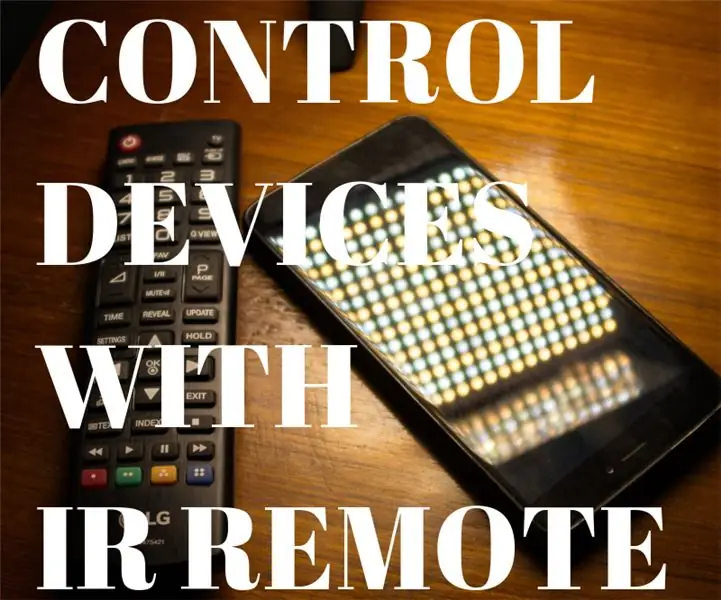
Sådan styrer du husholdningsapparater med fjernsyn med fjernbetjening med timerfunktion: Selv efter 25 års introduktion til forbrugermarkedet er infrarød kommunikation stadig meget relevant i de seneste dage. Uanset om det er dit 55 tommer 4K -fjernsyn eller dit billydsystem, har alt brug for en IR -fjernbetjening for at reagere på vores