Indholdsfortegnelse:
- Trin 1: Fusion360 -filer
- Trin 2: Udskriv test og opsætning
- Trin 3: 3D -udskrivning på et ledende stofspor
- Trin 4: Test af konduktivitet
- Trin 5: Udskrivning på forskellige overflader
- Trin 6: Flere udskrivningstest
- Trin 7: Læsemodstand
- Trin 8: Fastgør snapper igen med ledende epoxy
- Trin 9: Konklusion og næste trin
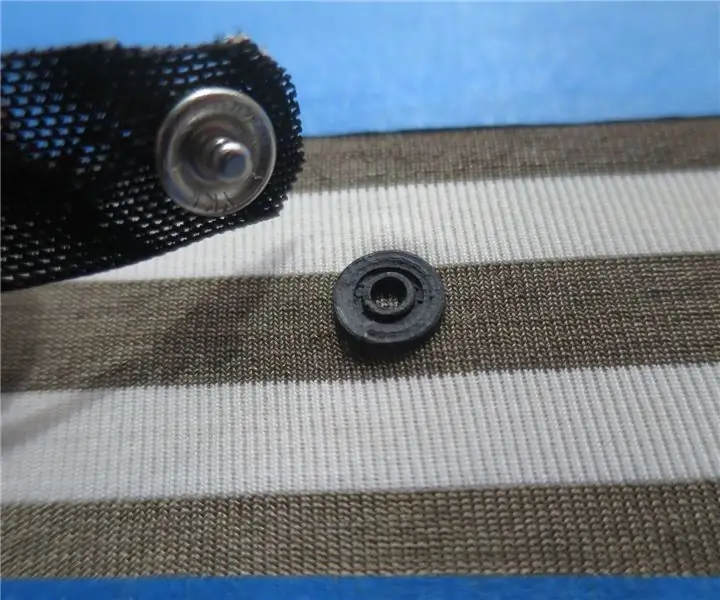
Video: Ledende snaps i 3D -udskrivning med Graphene PLA: 9 trin (med billeder)

2024 Forfatter: John Day | [email protected]. Sidst ændret: 2024-01-30 08:29
Af rachelfreirewww.rachelfreire.comFølg mere af forfatteren:
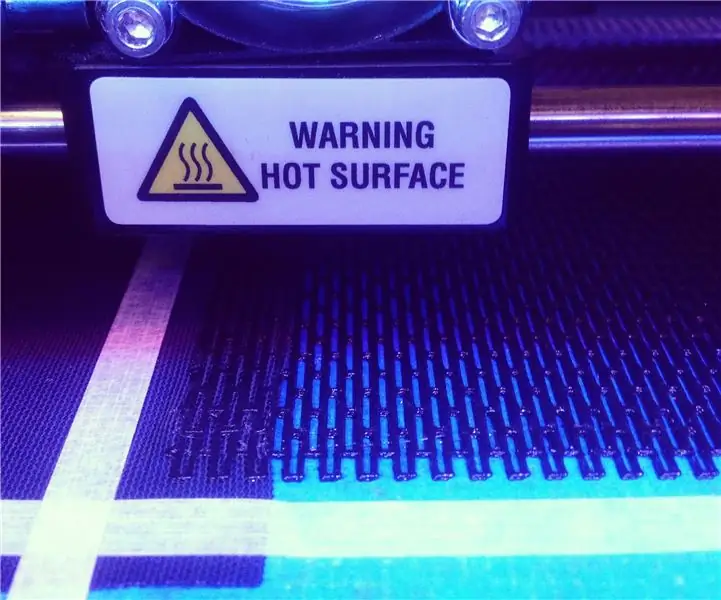
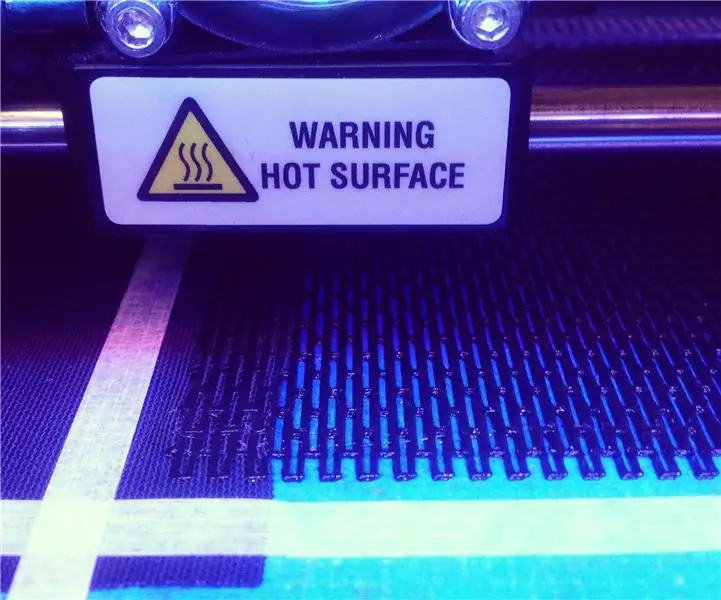
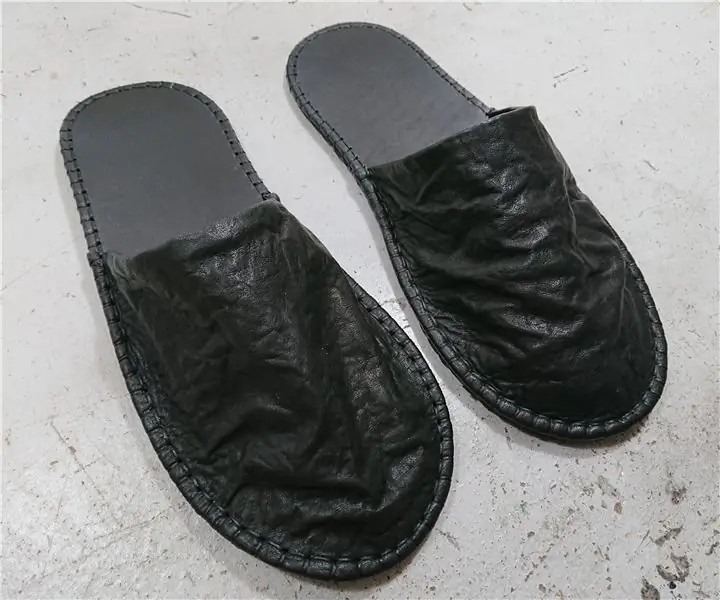
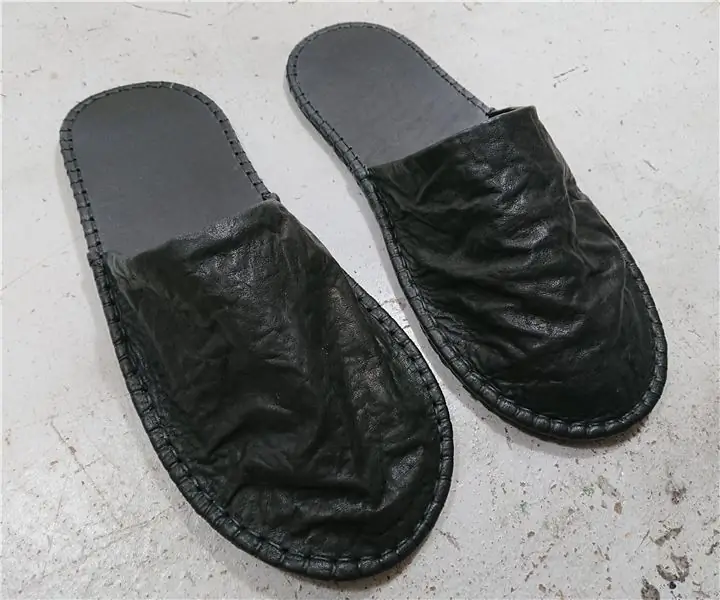
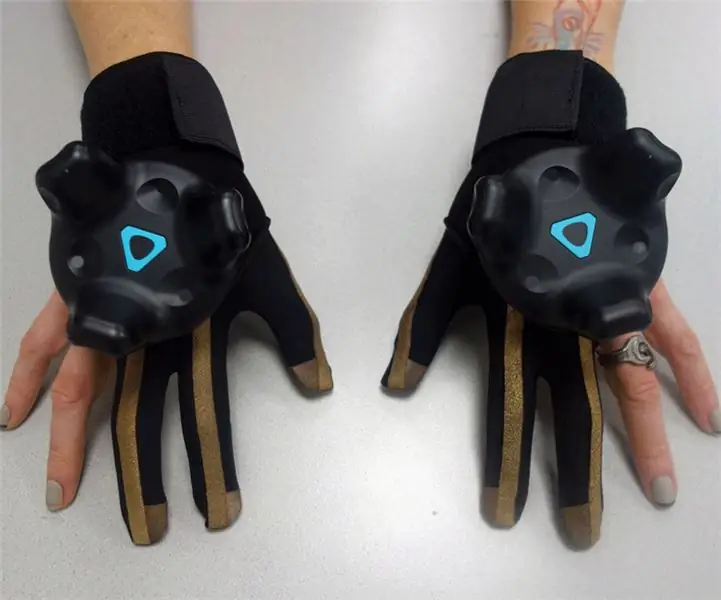
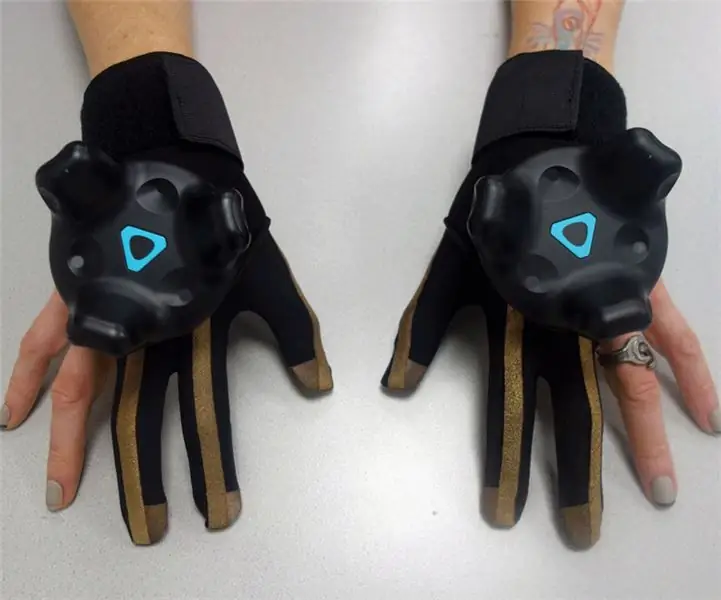
Om: designer, læder ninja, tech explorer, ruiner af manicure Mere om rachelfreire »
Denne instrukser dokumenterer mit første forsøg på at 3D -udskrive ledende snaps på stof. Jeg ville 3D -udskrive en kvindelig snap, der ville forbinde til en almindelig metalhane snap.
Filen blev modelleret i Fusion360 og udskrevet på en Makerbot Rep2 og en Dremel ved hjælp af Black Magic 3D ledende grafen PLA.
Snapsene er YKK 'Snapet' åbne stropsnaps (størrelse 12L) og er 7,5 mm på tværs. De bruges ofte af eTextiles praktiserende læger, da de er de mindste tilgængelige. Du kan købe dem i forskellige størrelser fra forskellige leverandører, men de ser ud til at være et standardiseret design. Køb størrelse 12 her.
Mit mål er at undersøge måder at lave et beklædningsgenstand, der er ledende og elastisk og helst ikke bruger hårde metaldele. At lave stik, der er kompatible med eksisterende købbare snaps, vil gøre det lettere at teste og gentage.
Denne test fungerede overraskende godt, og filen er værd at udskrive, men den har helt sikkert brug for meget mere tweaking. For nu kan den udskrives og testes som den er, men er bestemt et konceptbevis frem for et fuldt fungerende snap, som kan udskrives pålideligt f.eks. PLA har en tendens til at skrumpe, og snapsene har en begrænset levetid.
Hvis du udskriver denne fil, bedes du efterlade en kommentar og fortæl mig dine resultater !!
Flere billeder her:
Disse undersøgelser er en del af et større projekt kaldet Second Skin, en prototypedragt til eTextiles. Jeg vil uploade alle filer, mønstre og dokumentation, når de er færdige. Du kan følge projektet her eller via mit websted:
Du bør også tjekke Rewear af Lara Grant. Hun har arbejdet på et modulopbygget system til wearables baseret på et brødbræt med snaps 3D trykt på stof. Hun har også fokus på bæredygtigheden af disse teknikker, hvilket jeg også ser som integreret i deres fremtidige udvikling. Vi vil snart integrere vores eksperimenter i et dedikeret etextile connectors -websted, så sørg for at tjekke Laras websted og Instructables også!
Trin 1: Fusion360 -filer
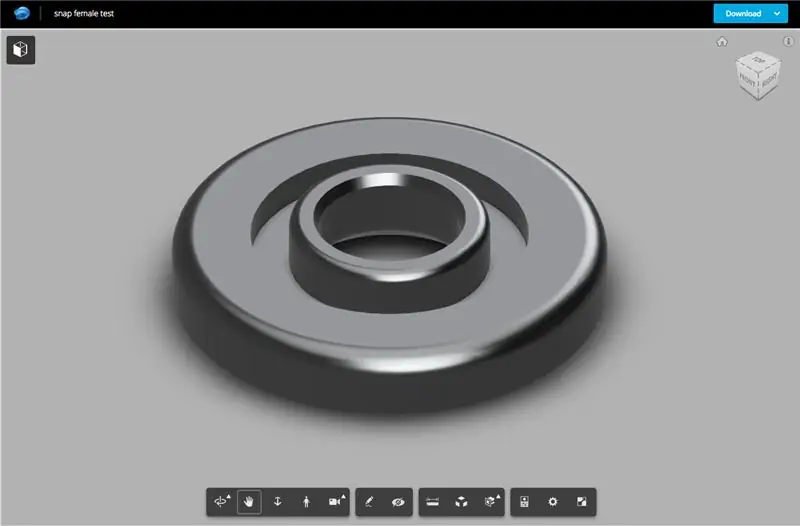
Filen blev modelleret ret hurtigt ved hjælp af Fusion360.
Jeg tog så mange målinger som muligt fra en eksisterende snap og lavede et groft design. Fordi snapsen er så lille, blev nogle af de indre proportioner lavet ved hjælp af gæt og derfor vil det have brug for mere leg.
Link til download af den aktuelle version her:
Filen vedhæftet denne instruktionsbog var mit første forsøg. Det fungerede ganske godt. Den linkede fil (ovenfor) blev tweaked, hvilket gjorde bunden af snap'en mere solid. tanken er, at det ville hjælpe det med at klæbe bedre til stoffet. Selvom dette hjalp noget, er begge filer stadig værd at teste, hvis du vil udskrive en version af dette. Jeg havde succes og fiaskoer med begge.
Jeg vil også påpege, at jeg er en total Fusion-nybegynder og havde ninja-hjælp til at tilpasse filen fra JON-A-TRON. Du bør helt tjekke hans 3D -printklasser!
Hvis du vil bruge større snaps (f.eks. 15 mm, som er mere almindelige), ville jeg forvente, at denne fil kan ændres i størrelse og udskrives med de korrekte dimensioner og også vil blive klikket på større versioner af dette snap -design. Jeg har ikke prøvet dette endnu, da jeg prøver at gøre alt så lille som muligt.
Disse metal snapets er fantastiske, men ofte er matricen svær at finde. Jeg bruger Prym vario tang til at påføre snaps i hånden, og det er svært at finde snap -matricen til at passe. Så jeg lavede en fusionsfil, der kan udskrives til 12L Snapets;) Igen er den ikke perfekt, da 3D -udskrifter har en tendens til at krympe og skæve og til sidst gå i stykker. Men jeg har lige printet nye, når dette sker! Filer er fastgjort til indersiden (stikdel) og udvendig (ringfæstning) dør. Den ene er en brøkdel større end den anden. Hvis du bruger dem den forkerte vej, stikker snappen fast i matricen.
Trin 2: Udskriv test og opsætning
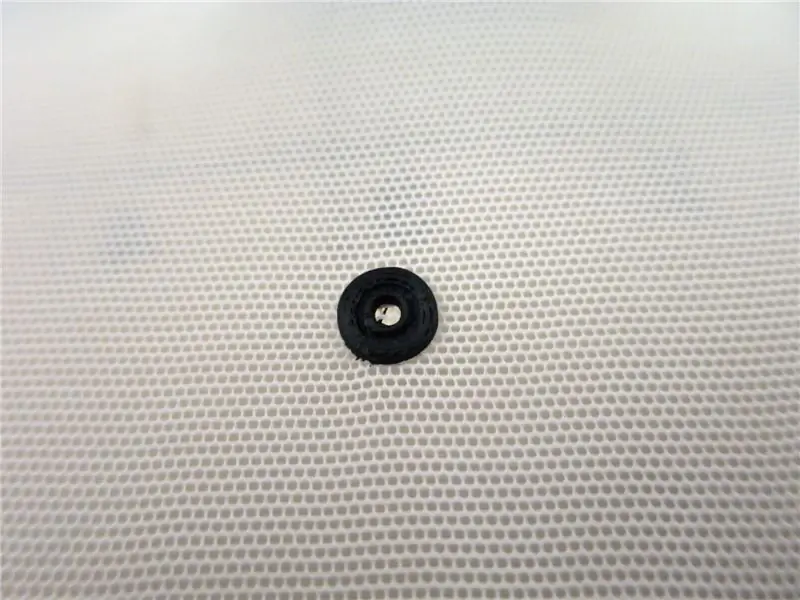
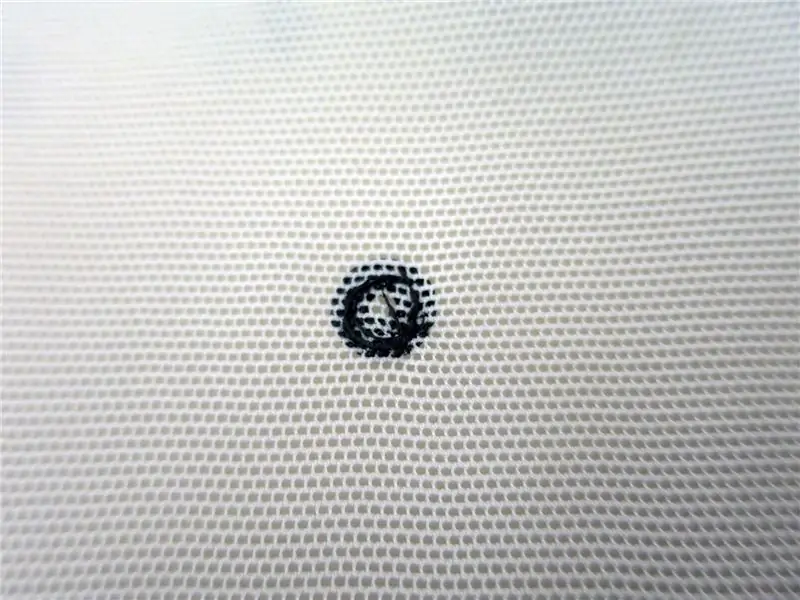
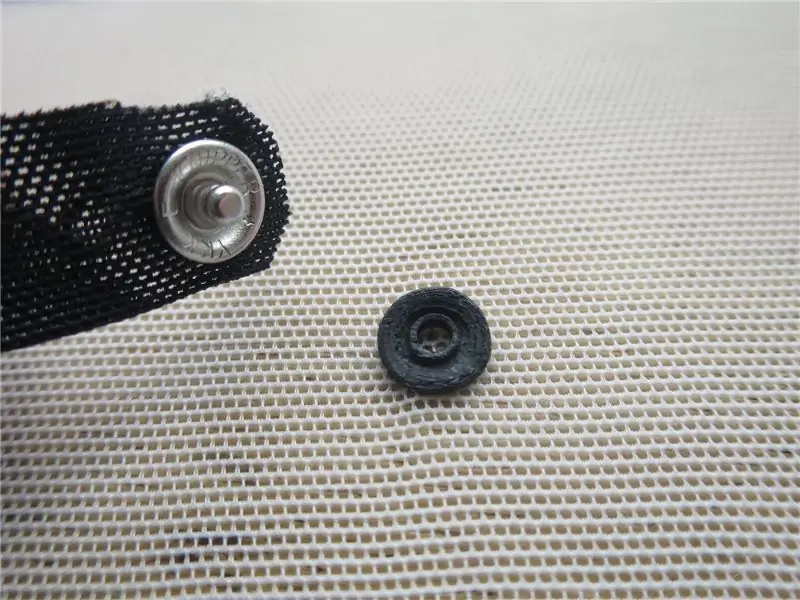
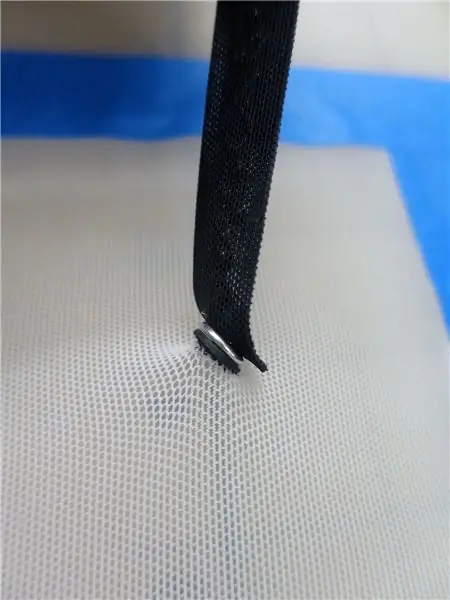
Denne første snap blev trykt af Lara Grant. Hun arbejder på et lignende projekt med at lave et snapstof og har en god instruktion om 3D -udskrivning på stof. Du bør også tjekke hendes wearables -klasser
Det er Black Magic 3D -grafenfilament og blev udskrevet på en Makerbot Rep 2 med udskrivningstemperatur og ekstruder indstillet til 220 °
Vi har begge testet en teknik, hvor du udskriver et bundlag af filament, sætter maskinen på pause for at indsætte stof og derefter fortsætter udskrivningen. Det betyder, at filamentet vil smelte omkring stoffet og skabe en forsegling. Du kan se dette på det andet billede; der er filament på stoffets underside. Dette lag blev først trykt på sengen, derefter blev printeren sat på pause, og stoffet blev indsat. Printeren blev derefter sat på pause, og udskrivningen fortsatte.
Det fungerede fantastisk! Første forsøg med at bruge den fil, jeg havde lavet 10 minutter tidligere.. Og den slog endda rigtig godt til!
Dette snap, du ser her, blev trykt på powernet. Det er et materiale, jeg bruger meget og bruger til det relaterede projekt Second Skin, der bruger stretchkredsløb. Det er 4 -vejs stretch og bruges til undertøj og dansetøj. Det fungerer godt, fordi det er et fint syntetisk net. Det er normalt lavet af polyamid, så filamentet smelter overfladen og klæber godt til det. Filamentet kan også smelte ind i og omkring overfladen af selve det mikrofine net.
Powernet har god trækstyrke, og hvis det spændes med tape, når du lægger det på sengen, bliver det ikke hængende af ekstruderen.
Trin 3: 3D -udskrivning på et ledende stofspor
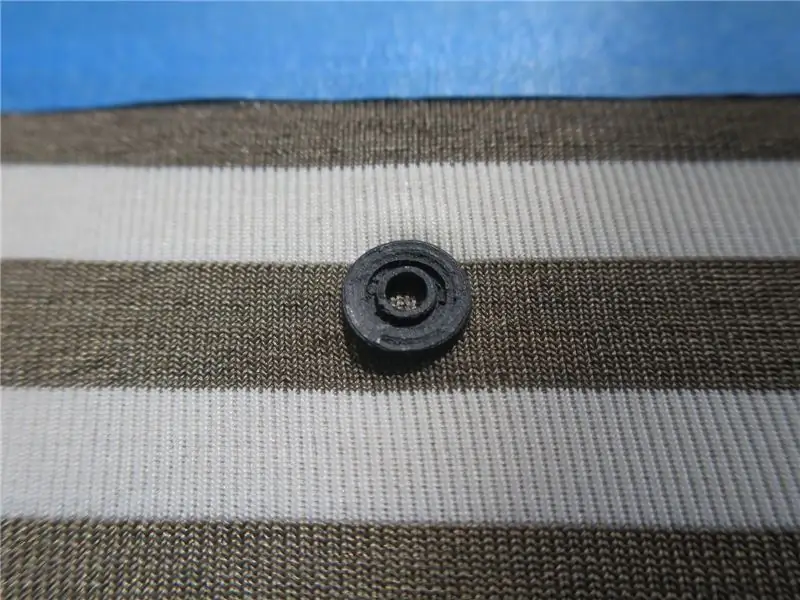
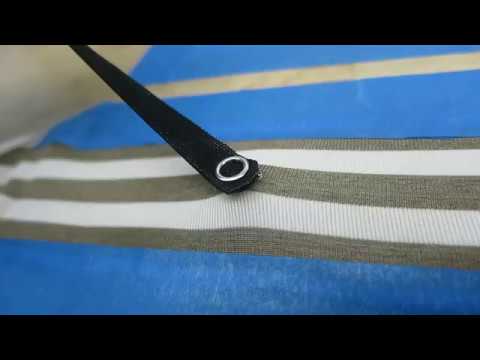
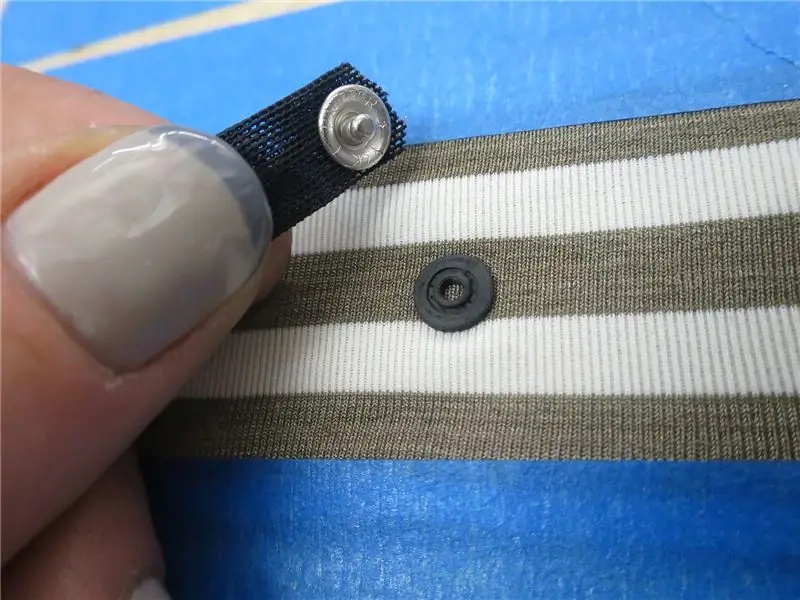
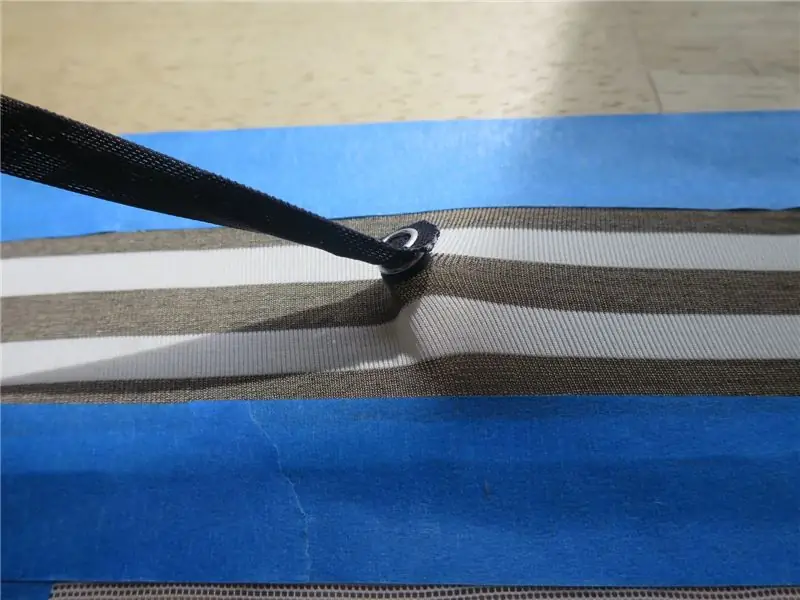
Dette strålende stof er en stretchjersey strikket med ledende spor. Jeg tror, det er trolddom fra Hannah Perner-Wilson og Mika Satomi fra Kobakant og blev specialfremstillet. Jeg fik nogle på eTextiles sommercamp, og vi besluttede, at dette ville være en god ting til at teste den elektriske forbindelse mellem stof og tryk.
Det er jerseystof, og det ser ud til, at fibrene blev belagt, før de blev vævet, frem for at den ledende belægning blev trykt på efter fremstilling. Det er for tykt til at udskrive gennem overfladen (som i den tidligere test), da filamentet ikke ville forbinde på samme måde som det gør gennem hullerne i powernet.
Vi satte Makerbot til at printe lige oven på stoffet. hvad du ser ovenfor er det første testprint på dette materiale.
Mange forskellige mennesker har testet 3D -print på stof, og det ser ud til at variere afhængigt af printets art, de anvendte materialer og maskiner. De fleste succeser ser ud til at involvere masker, da vævningen er løs, og filamentet kan synke gennem stoffet for at skabe en binding.
Nogle mennesker sænker printerens dyse. Dette smadrer ekstruderen ind i stoffet og tvinger filament ind i fibrene, men kan trække materialet. En anden mulighed er at hæve ekstruderens startpunkt for at starte udskrivningen, hvilket betyder at du skærer udskriften på en sådan måde, at den starter lige over tykkelsen af stoffet. Jeg forestiller mig, at dette ville fungere godt, hvis dit stof var tykt. Da vores er ret tynde og flade, printede vi lige på materialet med standardindstillingerne, bare ved at slukke for tømmerflåder og enhver understøttelse.
Det fungerede smukt! Dette kan have været på grund af forskellige faktorer:- overfladen af dette særlige stof var ideel til tryk til at hæfte- ekstruderen var tilfældigvis ved den perfekte temperatur på dette tidspunkt (dette filament kan være meget inkonsekvent)- guderne af 3D -print var i godt humør, og vi var super heldige
Det er klart, at dette kræver mere test.
Trin 4: Test af konduktivitet

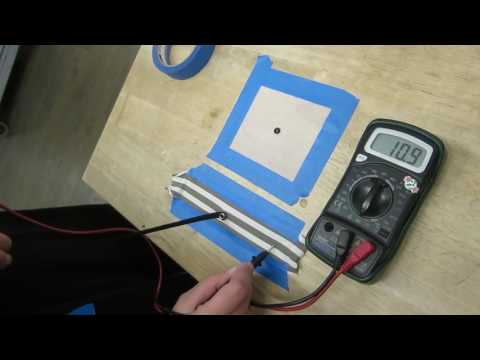
Denne test brugte et stretch eTextile -stik fremstillet med Karl Grimm ledende gevind. Inde i det sorte stik er der en zigzag af ledende tråd isoleret af stoflag på hver side. Hver ende har en han -snapet. Alle disse materialer har ganske lav modstand.
Modstanden på tværs af 30 cm -stikket, gennem snap og på tværs af omkring 8 cm ledende stof synes at være omkring 10 ohm. Dette var overraskende og syntes at forblive ret stabilt, selv når det var strakt. Jeg er ikke sikker på, at dette er en nøjagtig og gentagelig læsning!
Trin 5: Udskrivning på forskellige overflader
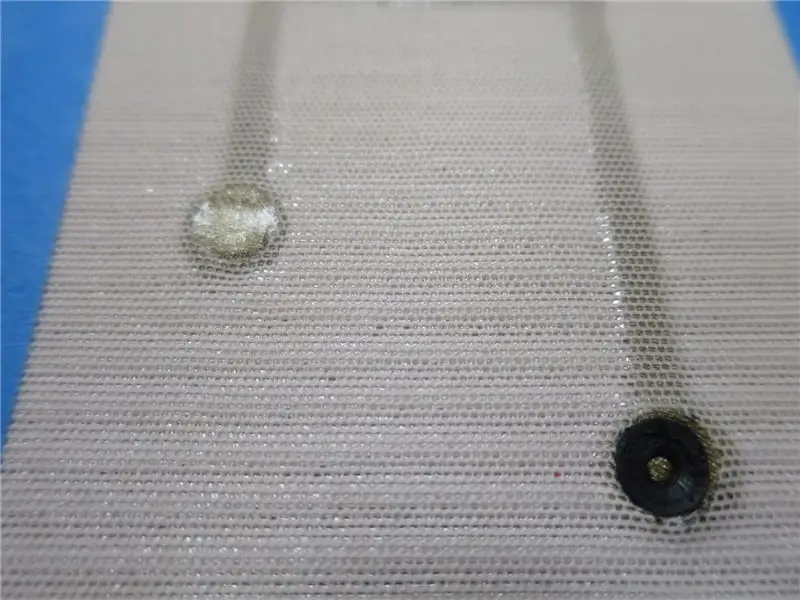
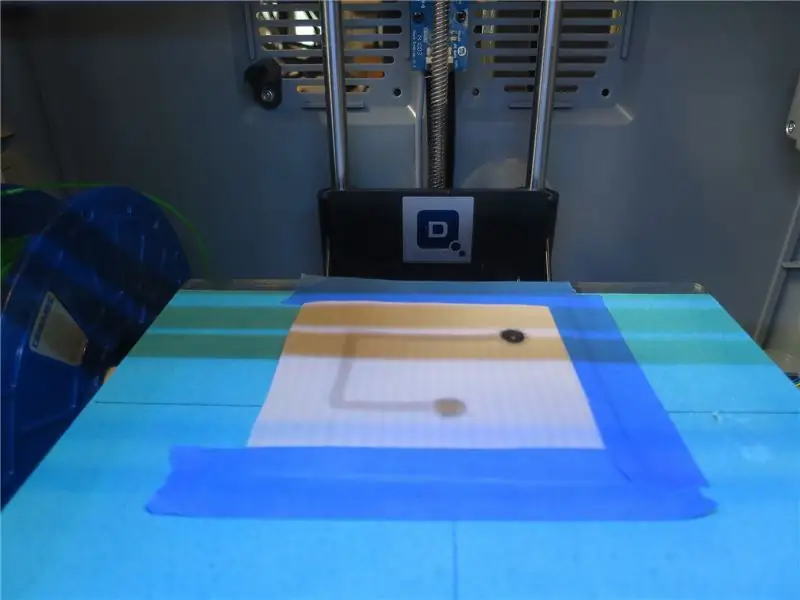
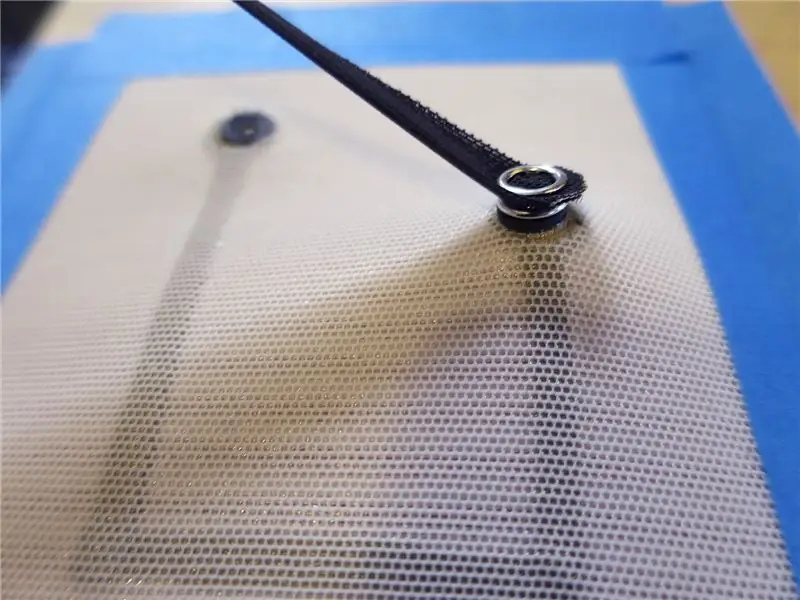
Derefter besluttede jeg at prøve at udskrive på en Dremel. Dette skyldes hovedsageligt, at Makerbot havde en hvæsende pasform, men variationen er altid god. Igen blev udskrivningstemperaturen og ekstruderen indstillet til 220 °
Jeg har arbejdet med bundne, isolerede, elastiske ledende spor til eTextiles. Disse stoffer anvender bundne tekstillag med Bemis SewFree fusion, en superfin varmebindende film. Det betyder, at stofprøverne var tykkere end de tidligere tests. De ledende spor er isoleret inde i powernet -stof og har kun enderne udsat som runde puder.
Da jeg først udskrev filen med standardindstillinger, smadrede den ind i stoffets overflade og forvrængede udskriften. Du kan se resultatet i det første billede. Snap fungerede ikke denne gang.
Jonathon viste mig, hvordan jeg skærer filen i Cura og hæver ekstruderens startposition med 0,4 mm.
Til den næste test tilføjede jeg også et lag SewFree -limning til den overflade, jeg skulle udskrive på. Dette var for at se, om dette gjorde nogen forskel for, hvordan trykket klæbte.
Det fungerede i første omgang rigtig godt, som du kan se på det sidste billede. Desværre efter et par snaps, løsnede snapet fra stoffet og faldt af.
Trin 6: Flere udskrivningstest
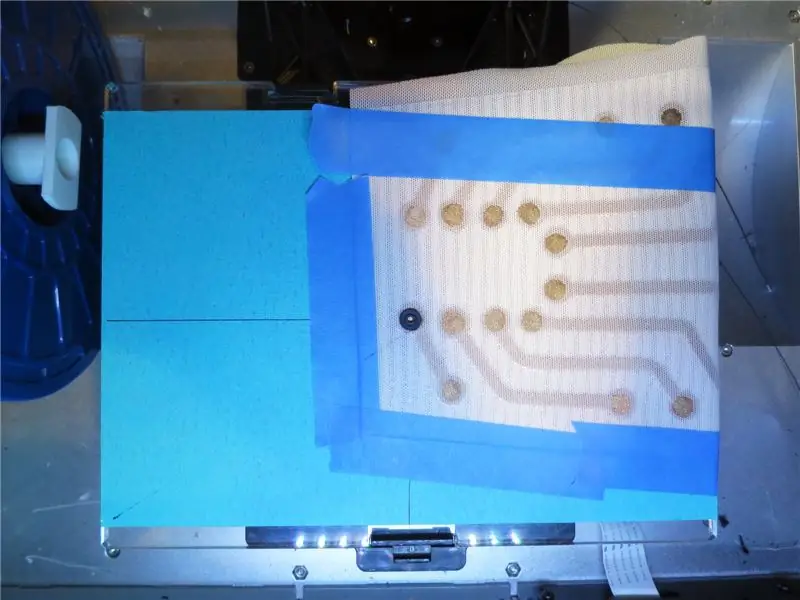
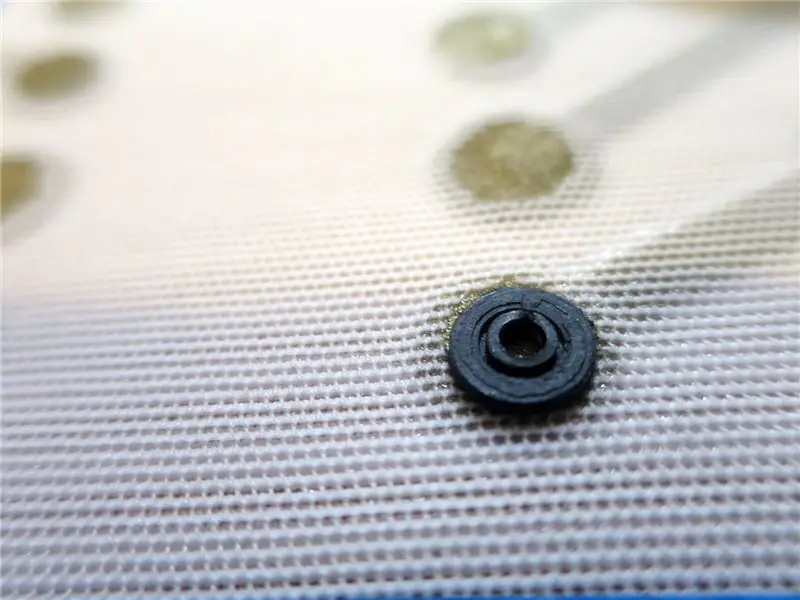
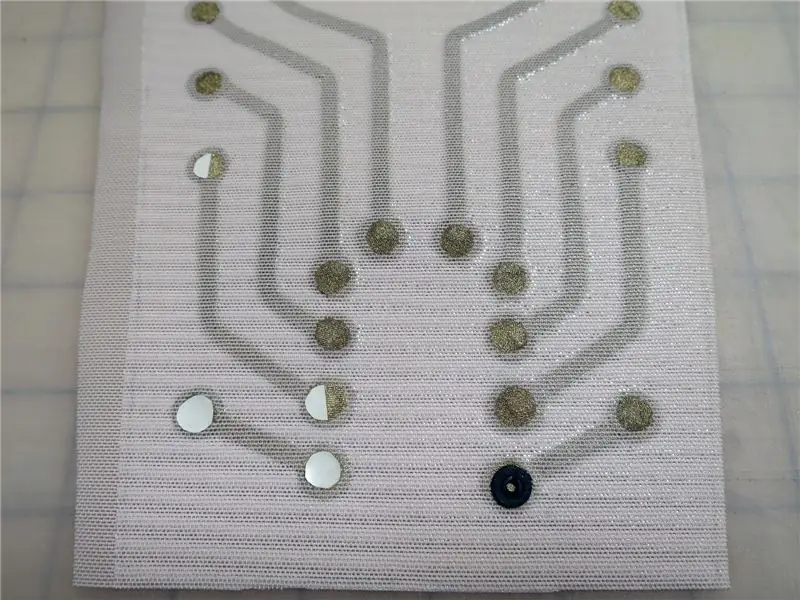
Jeg forsøgte derefter at udskrive flere snaps for at se, hvordan strømmen flød gennem to snaps i hver ende af et ledende spor. Da jeg kun havde et enkelt snap på den forrige test, kunne jeg ikke kontrollere. Måske var det tryk, Lara havde lavet tidligere, en tilfældighed. Jeg lavede et hurtigt panel for at prøve flere udskrifter.
Da dette var en test, besluttede jeg, at jeg ville udskrive hver enkelt snap individuelt i stedet for at prøve at udskrive flere snaps på et stykke stof.
Tre grunde: 1. Jeg ville ikke investere tid i at lave en layoutfil, da stofkredsløbet, jeg printede på, blev lavet upræcist2. Udskrifterne fejler ofte 3. Jeg ville ikke have, at useriøs filament trak hen over stoffet
Jeg lagde hvert snap op til et centraliseret punkt og printede dem en efter en. Hver enkelt kom perfekt ud.
Jeg tilføjede SewFree fusing til nogle af de ledende puder. Du kan se dette på billederne som hvide cirkler og halvcirkler. Dette er papirunderlaget, der bliver skrællet væk. Jeg lod den stå på, så det er lettere at se på billederne. Jeg tænkte, at det ville være godt at se, hvordan fusionen påvirkede vedhæftningen på tværs af det samme tryk. De blev alle ret ens. De fleste sad fast, og et par faldt af. Ikke sikker på hvorfor, men jeg antager, at det skyldes små forskelle i tykkelsen af stoflaget. De blev alle udskrevet hurtigt efter hinanden på den samme printer med de samme indstillinger.
modstanden over et 15 cm ledende spor gennem to resistive snaps var omkring 50 ohm. Dette blev udført umiddelbart efter udskrivning og virkede super ledende, så vi havde brug for flere tests.
Trin 7: Læsemodstand
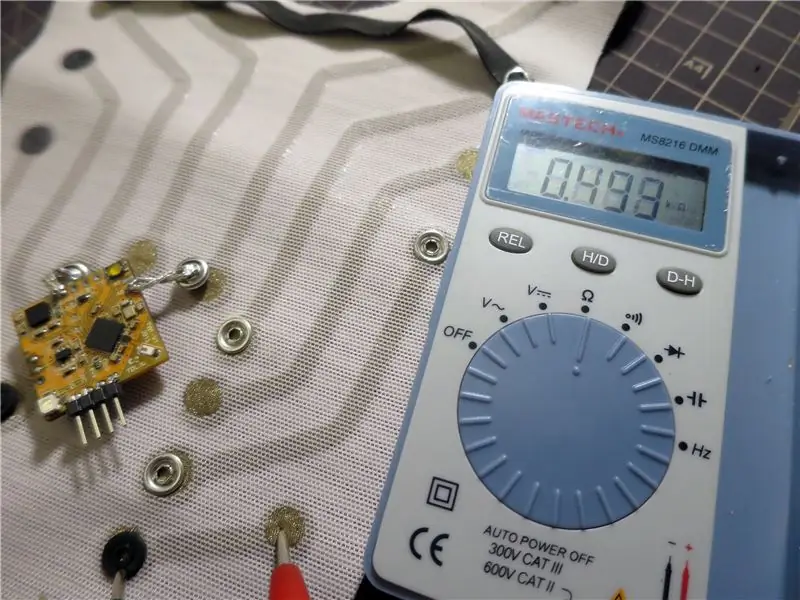
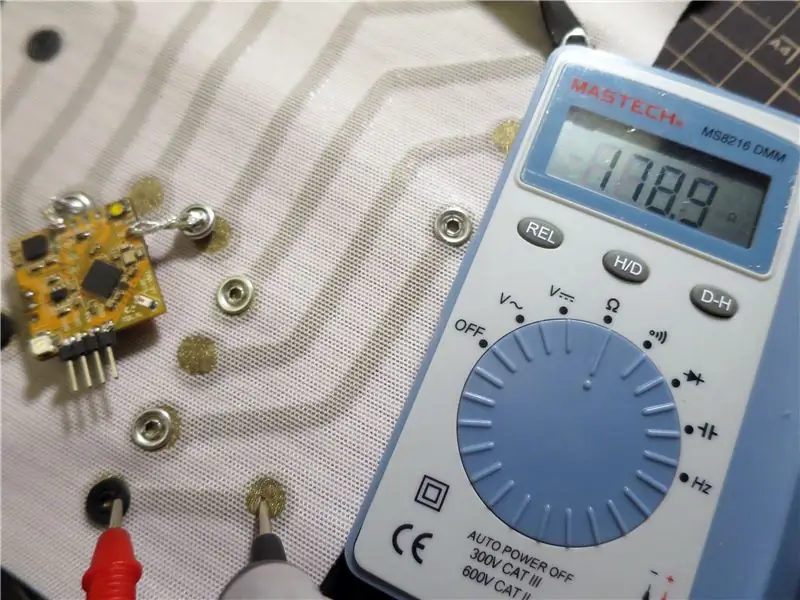
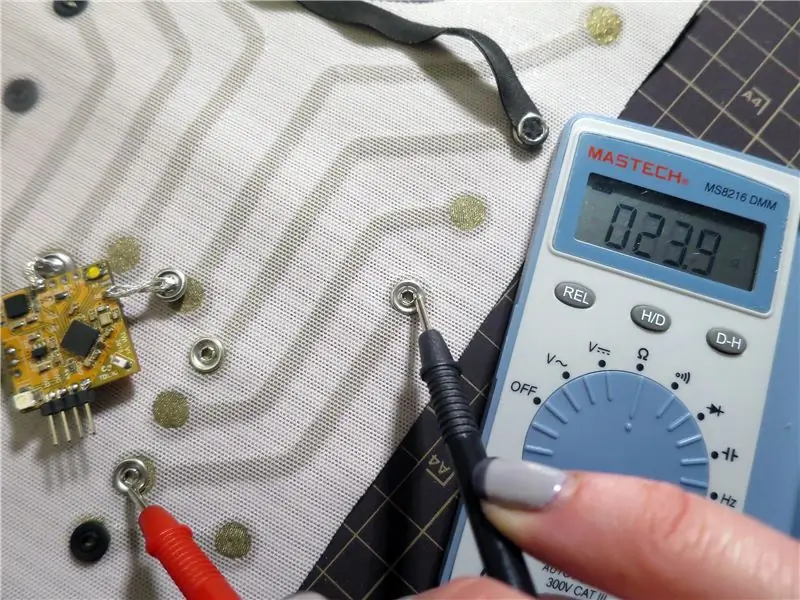
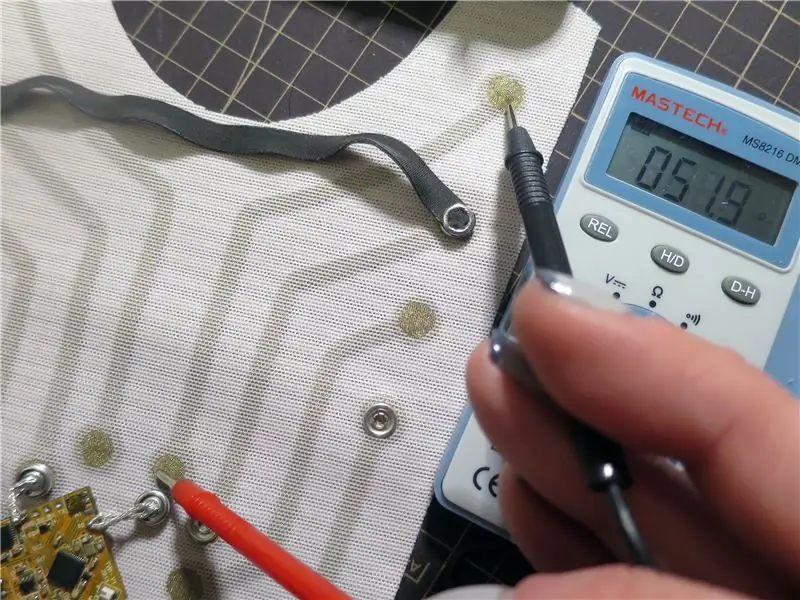
De målinger, jeg tog fra snapsene, syntes at var meget forskellige. Dette ændrede sig også over tid.
Trin 8: Fastgør snapper igen med ledende epoxy
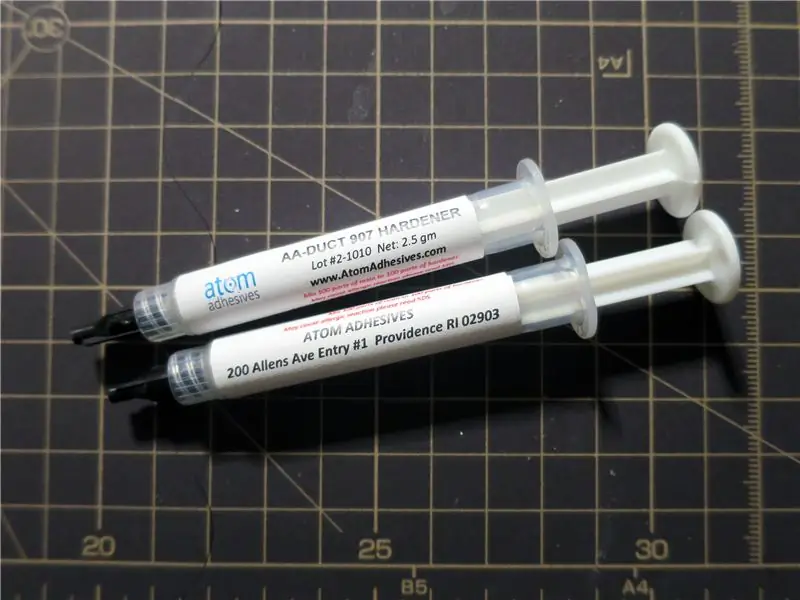
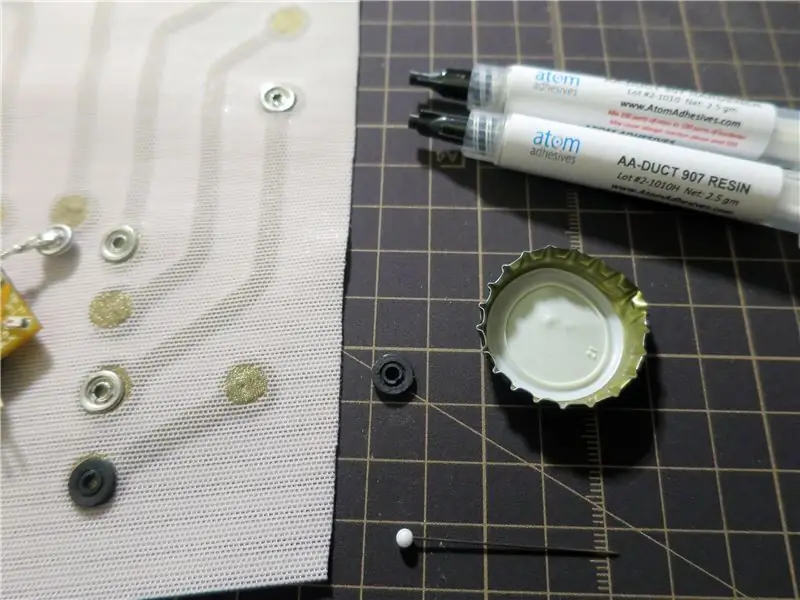
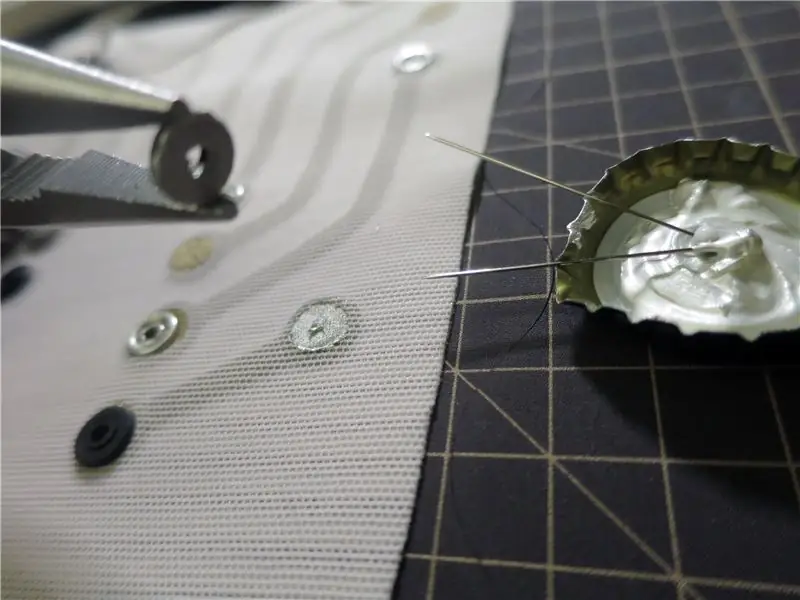
Nogle af snapperne faldt af efter lidt brug. De klæbte sig ikke så godt til det tætbundne materiale som ved de tidligere tests.
På dette tidspunkt er det værd at undersøge en anden mulighed: Kan snapsene udskrives og derefter sidde fast på stoffet bagefter.
Det kan være rigtigt, at snaps kan udskrives på visse stoffer, men skal limes til andre. Dette kan stadig være en brugbar mulighed.
Jeg brugte ledende epoxy og limede to af snapsene tilbage på plads for at se, om limen kan danne en binding og føre pålideligt.
Desværre klæbte dette slet ikke godt til stoffet. Epoxyen er ret kridtet og kan ikke lide det tætte syntetiske materiale. Selvom limen tillod en lille mængde strøm at flyde, faldt snapsene af efter et snap.
Trin 9: Konklusion og næste trin
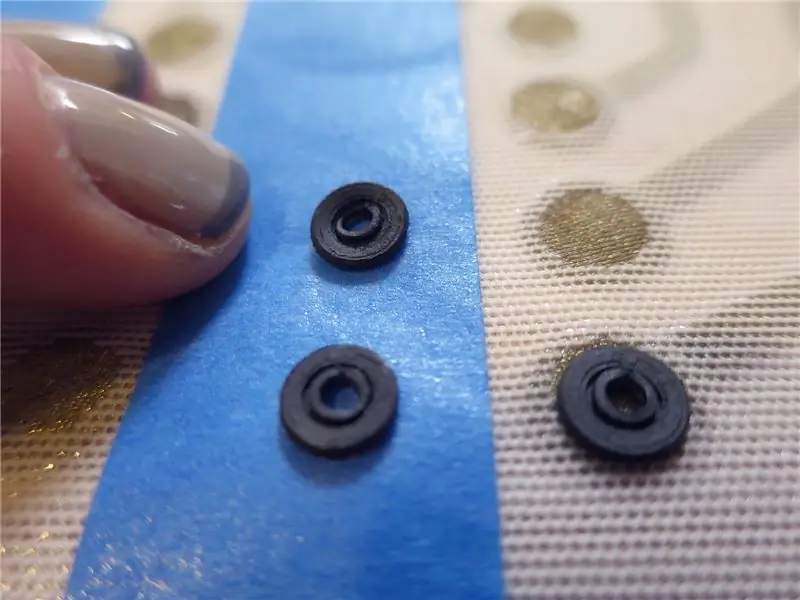
Dette snap -design fungerede rigtig godt til en første test. Det klikker sikkert, kan lede en lille mængde strøm og er et godt bevis på konceptet.
Desværre gav de ikke konsekvent ledningsevne. Nogle var ok, og andre virkede slet ikke. Det ser ud til at det er et problem at bruge tætvævet stof, så det fungerer ikke så godt for mine bindede stoffer. Brug af mere åben vævning som trøjen, og især powernet virker den bedste løsning. Problemet med det er, at jo mindre tæt et stof er, desto værre er ledningsevnen for etextiler.
Der er en hel del praktiske problemer med PLA. Det har en tendens til at deformere og krympe. Nogle af snapsene virkede med det samme, nogle havde brug for et par indledende tvungen lukninger, før de ville overholde, tilsyneladende for at strække trykket lidt. Nogle virkede for små til overhovedet at snappe.. Det hele var lidt inkonsekvent.
Jeg har også læst, at ledningsevnen for disse materialer kan ændre sig over tid. I dette tilfælde vil jeg sige, at trykket ved selve snappen kan påvirke dette. Også løbende strøm gennem snap kan øge modstanden permanent. Dette vil helt sikkert indebære mere test.
der er et ret godt overblik over Black Magic 3D -filamenter her
Jeg vil bruge denne snap -idé i et handskedesign. Jeg vil finde en måde at lave aftagelige stik til strækningssensorer på. Ideen ville være, at denne snap -fil kan integreres direkte i en 3D -printet sensor for at forbinde den til et kredsløb.
I gennemgangen fandt jeg denne proces interessant og informativ. Det er ikke stabilt nok til at producere konsistente målbare resultater, og jeg vil gerne undersøge nærmere i mere kontrollerede eksperimenter.
Hvis du prøver nogle af disse udskrifter, bedes du efterlade en kommentar!
Anbefalede:
Fremstilling af elektronisk lyd med ledende gips: 9 trin (med billeder)
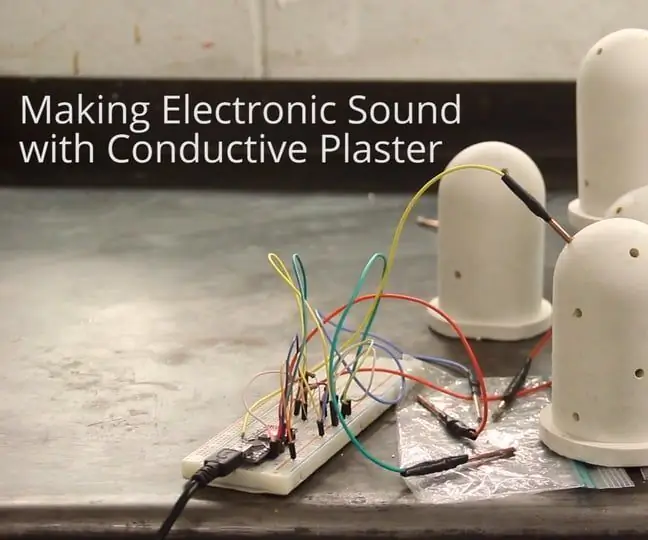
Lav elektronisk lyd med ledende gips: Efter blorggggs projekt om ledende silikonkredsløb besluttede jeg at gå på mit eget eksperiment med kulfiber. Det viser sig, at en form, der er støbt ud af kulfiberinfunderet gips, også kan bruges som en variabel modstand! Med et par kobberstang og
Ledende lim og ledende tråd: Lav et LED -display og stofkredsløb, der ruller op: 7 trin (med billeder)
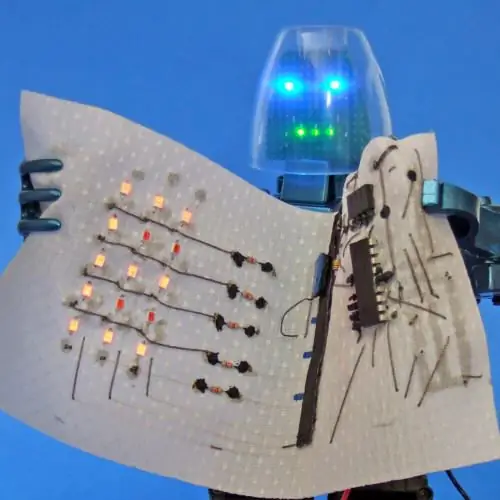
Ledende lim og ledende tråd: Lav et LED -display og stofkredsløb, der ruller op.: Lav dine egne ledende stoffer, tråd, lim og tape, og brug dem til at lave potentiometre, modstande, kontakter, LED -displays og kredsløb. Brug af ledende lim og ledende tråd kan du lave LED -displays og kredsløb på ethvert fleksibelt stof
Angelina smeltbare fibre med ledende tråd: 11 trin (med billeder)
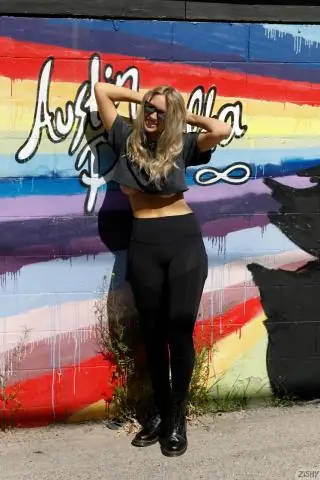
Angelina smeltbare fibre med ledende tråd: En metode til fastgørelse af ledende tråd til stof. Vil du have flere eTextile How-To DIY eTextile-videoer, selvstudier og projekter? Besøg derefter The eTextile Lounge
Smeltet stof med ledende tråd: 9 trin (med billeder)
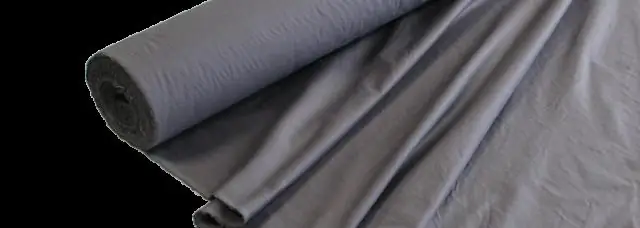
Smeltet stof med ledende tråd: En metode til fastgørelse af ledende tråd til stof. Vil du have flere eTextile How-To DIY eTextile-videoer, selvstudier og projekter? Besøg derefter The eTextile Lounge
Sådan sys med ledende tråd med Diana Eng: 10 trin (med billeder)
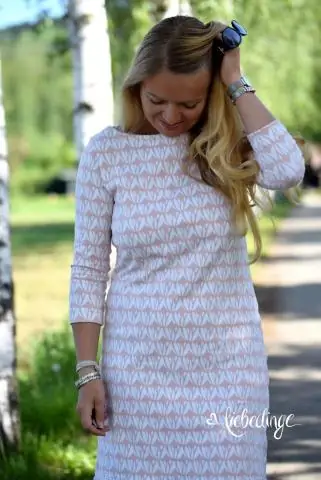
Sådan sys med ledende tråd med Diana Eng: Kombination af elektricitet og mode! Sværhedsgrad: Stadig læring Tidslængde: 45 minutter Materialer: beklædningsgenstand til syning, ledende tråd, saks, to lysdioder, CR2032 urbatteri, BS7 batteriholder, forsvinder blækpen , nål-næsetang, r