Indholdsfortegnelse:
- Trin 1: Designproces
- Trin 2: Drivlinje
- Trin 3: Ribbeholder
- Trin 4: Elektronik
- Trin 5: Færdig bord og promoveringsvideo
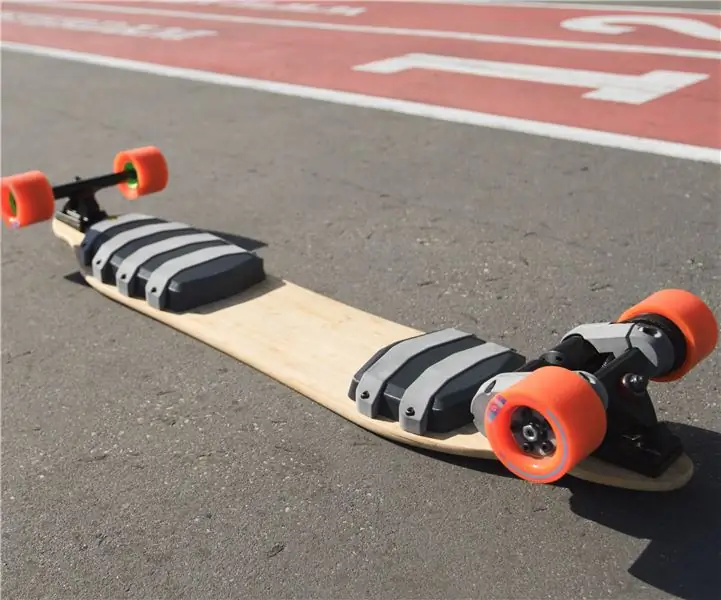
Video: Fusion Board - 3D -printet elektrisk skateboard: 5 trin (med billeder)

2024 Forfatter: John Day | [email protected]. Sidst ændret: 2024-01-30 08:29
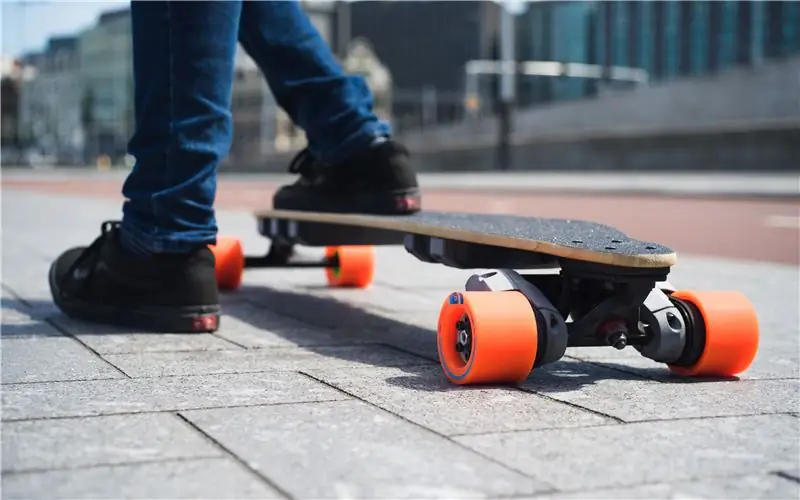
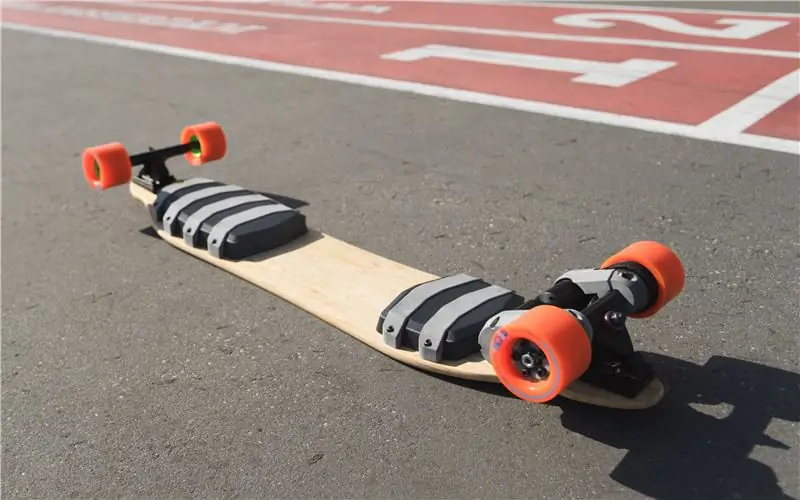
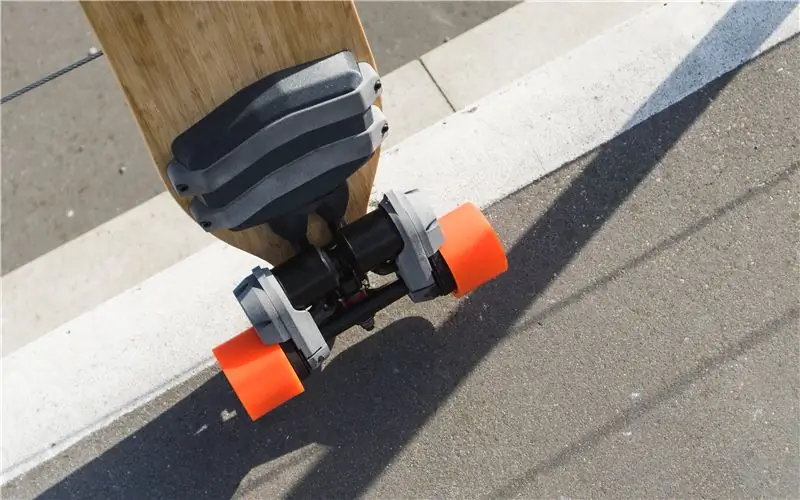
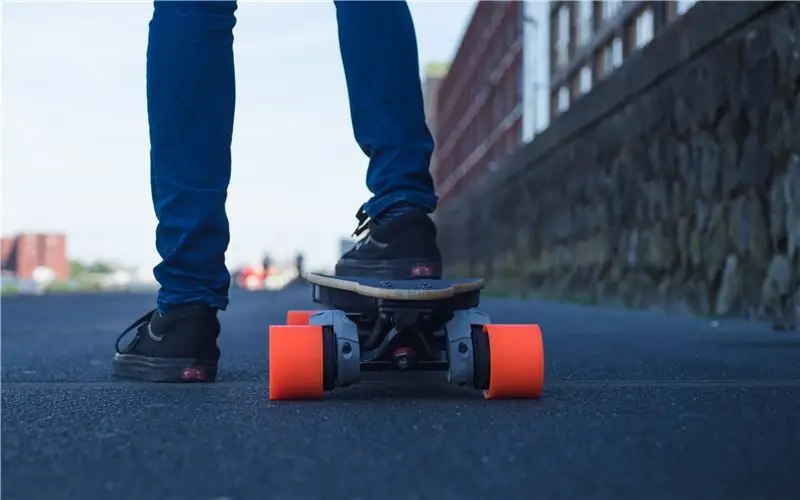
Denne Instructable er en oversigt over byggeprocessen for Fusion E-Board, som jeg designede og byggede, mens jeg arbejdede på 3D Hubs. Projektet fik til opgave at promovere den nye HP Multi-Jet Fusion-teknologi, der tilbydes af 3D Hubs, og vise flere 3D-printteknologier frem, og hvordan de effektivt kan kombineres.
Jeg designede og byggede et elektrisk motoriseret longboard, som kan bruges til korte til moderate rejser eller kombineret med offentlig transport for at tilbyde et meget bredere rejseområde. Den har en høj topfart, er meget manøvredygtig og let at bære, når den ikke er i brug.
Trin 1: Designproces
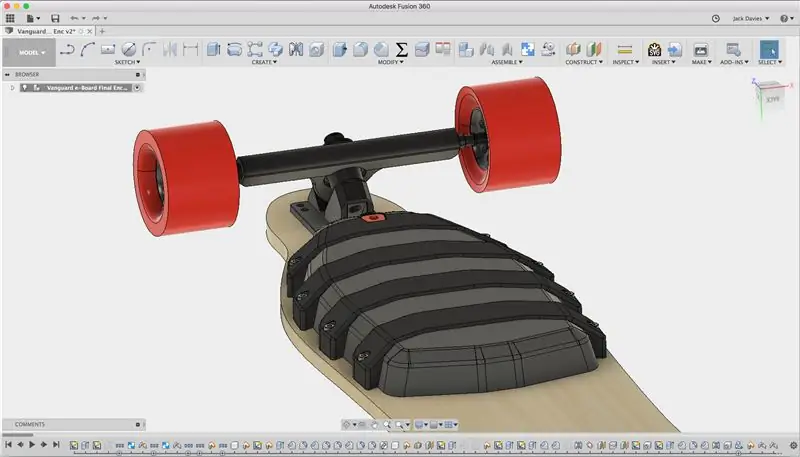
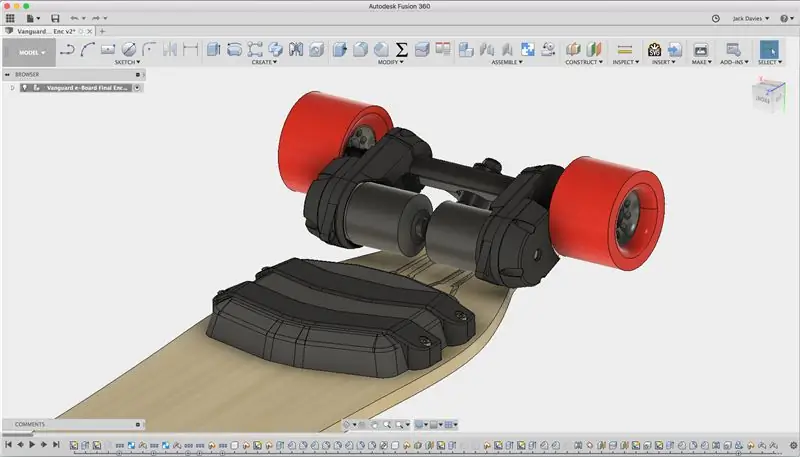
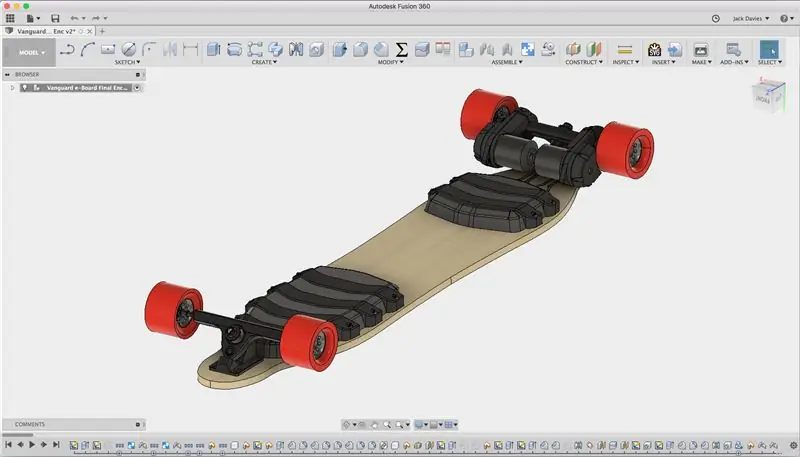
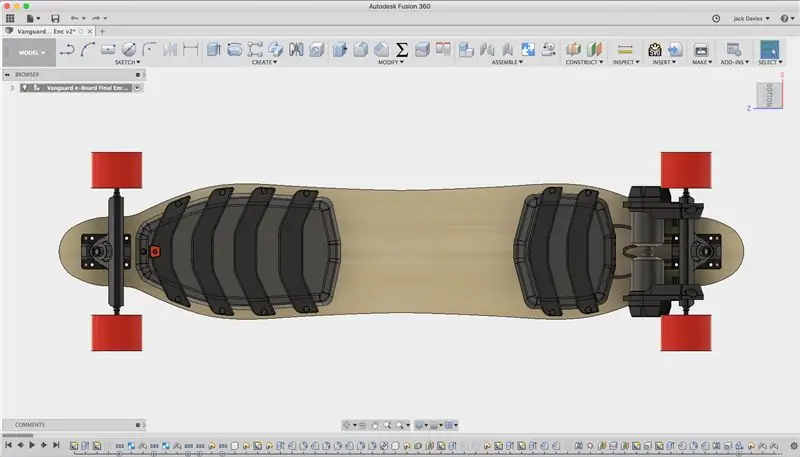
Jeg startede projektet med at identificere de vigtigste standardkomponenter i longboardet; lastbiler, dæk og hjul. Disse var fra hyldens dele, så jeg brugte dem som udgangspunkt for designet. Den første fase var at designe drivlinjen, dette inkluderer motorophæng, gearopsætning og inkluderede nogle ændringer af lastbilerne. Størrelsen og placeringen af motorophængene ville diktere størrelsen og placeringen af kabinetterne, så det var vigtigt, at dette blev afsluttet først. Jeg beregnede den ønskede tophastighed og momentkrav, som derefter gjorde det muligt for mig at vælge motorer og batteri til tavlen. Gearforholdet blev også beregnet, og remskivestørrelserne blev valgt sammen med drivremlængden. Dette gjorde det muligt for mig at regne ud den korrekte størrelse på motorophængene, hvilket sikrede et godt spændt bælte.
Det næste trin var at designe batteri- og hastighedsregulator (ESC) kabinetter. Det valgte dæk består overvejende af bambus, så det er ret fleksibelt og bøjer væsentligt i midten. Dette har fordele ved at være behagelig at køre, da det absorberer stødene på vejen og ikke overfører dem til rytteren. Dette betyder imidlertid også, at der er behov for et delt kabinet for at huse batteriet og elektronikken, da et kabinet i fuld længde ikke ville være i stand til at bøje med kortet og ville komme i kontakt med jorden under drift. De elektroniske hastighedsregulatorer (ESC) blev placeret tættest på motorerne på grund af elektriske begrænsninger. Fordi motorerne er fastgjort via lastbilerne, ændres positionen under sving, så kabinettet skulle være designet til at muliggøre frigivelse af motorerne.
Batterisystemet blev placeret i den anden ende af dækket og husede elektronikken relateret til strøm. Dette omfattede batteripakken, der består af 20 lithium -ion 18650 celler, batteristyringssystemet, tænd/sluk -kontakt og opladningsstik.
Jeg brugte Autodesk Fusion360 til hele designprocessen, denne software gjorde det muligt for mig hurtigt at modellere komponenter inde i hovedkonstruktionen, hvilket fremskyndede udviklingstiden betydeligt. Jeg brugte også simuleringsfunktionerne i Fusion360 for at sikre, at delene ville være stærke nok, især motorophængene. Dette gjorde det muligt for mig at faktisk reducere størrelsen på beslagene, da jeg kunne verificere kravene til styrke og afbøjning og fjerne materiale, mens jeg stadig opretholder en passende sikkerhedsfaktor. Efter at designprocessen var afsluttet, var det meget let at eksportere de enkelte dele til 3D -print.
Trin 2: Drivlinje
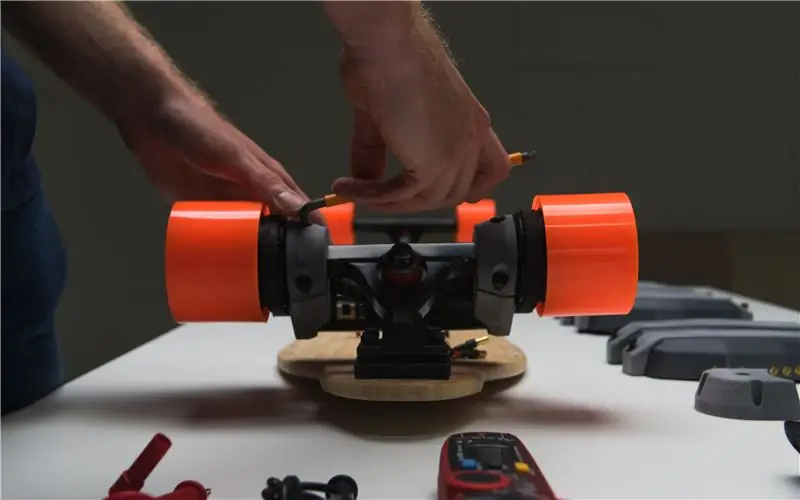
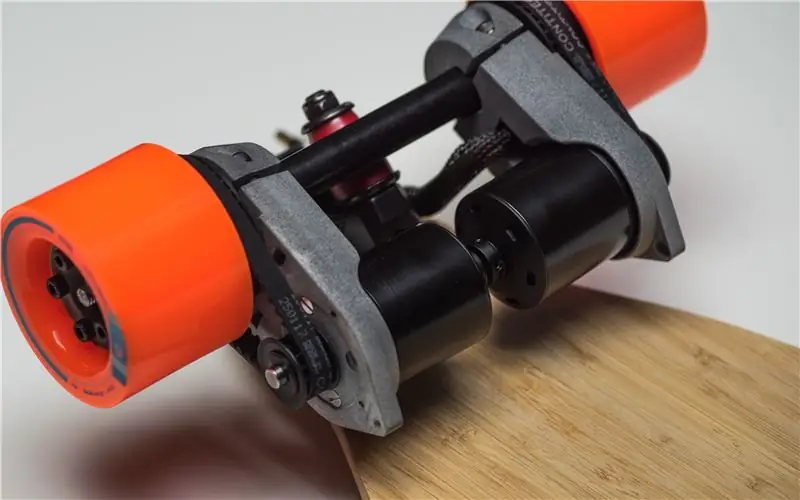
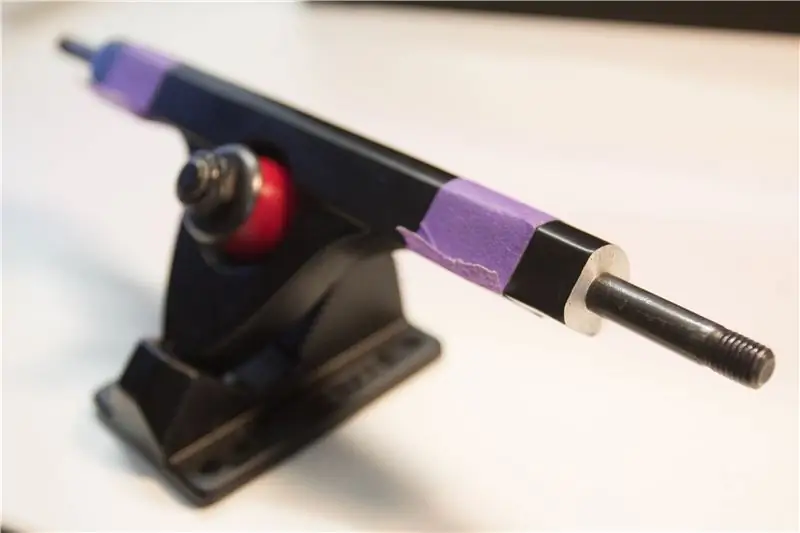
Jeg færdiggjorde først opbygningen af drivlinjen for at sikre passende afstand til elektronikhuset. Jeg valgte Caliber -lastbiler til brug, da de har en firkantet profil, der var perfekt til at spænde motorophængene på. Men akslen var lidt for kort til at de to motorer kunne bruges på den samme lastbil, så jeg var nødt til at forlænge denne for at hjulene kunne passe.
Jeg opnåede dette ved at skære nogle af aluminiums lastvognens bøjlehus op og afsløre mere af stålakslen. Jeg skar derefter det meste af akslen ned og efterlod omkring 10 mm, som jeg derefter kunne gevind med en M8 -dør.
En kobling kunne derefter skrues på og tilføjes en anden gevindaksel, der effektivt forlængede akslen. Jeg brugte Loctite 648 fastholdelsesmasse til permanent at fastgøre koblingen og den nye aksel for at sikre, at den ikke skrues af under brug. Dette tillod de to motorer at passe på lastbilen og gav masser af afstand til hjulene.
Drivbanen blev primært trykt ved hjælp af HP Multi-Jet Fusion-teknologi for at sikre stivhed og styrke under høj acceleration og bremsning, hvor de største kræfter ville blive overført.
En særlig remskive blev designet til at låse fast i baghjulene, som derefter blev forbundet til motorhjulet med et HTD 5M -bælte. Et 3D -trykt cover blev tilføjet for at beskytte remskivenheden.
Trin 3: Ribbeholder
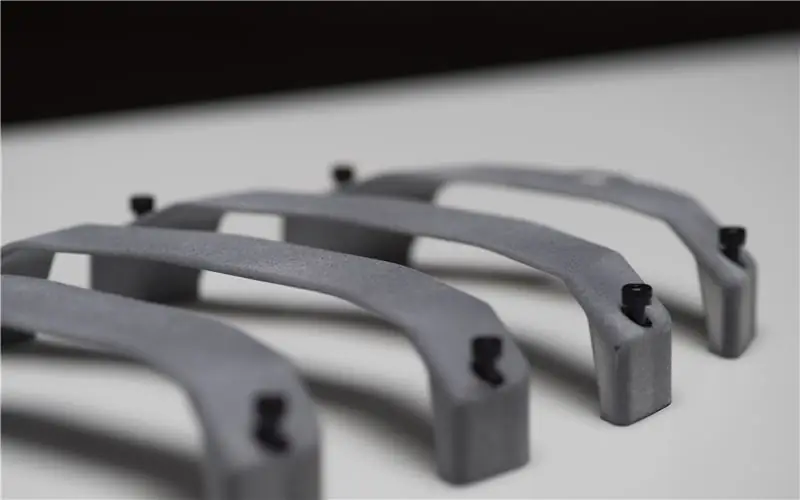
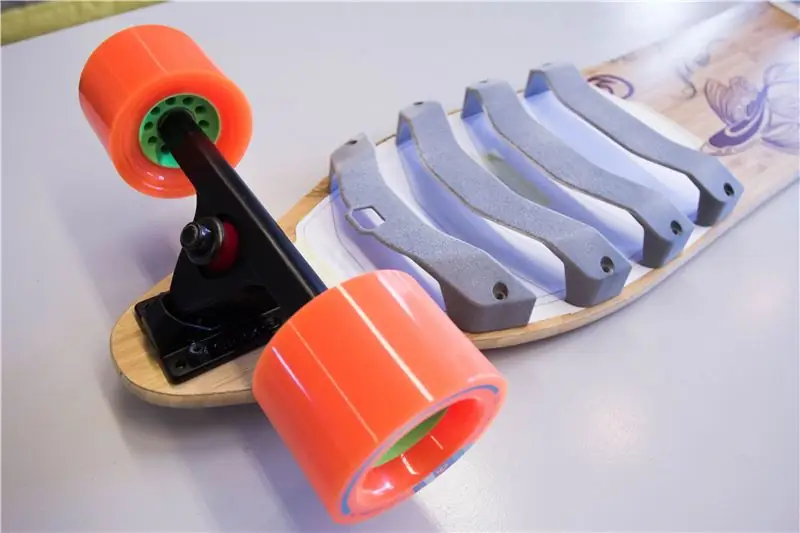
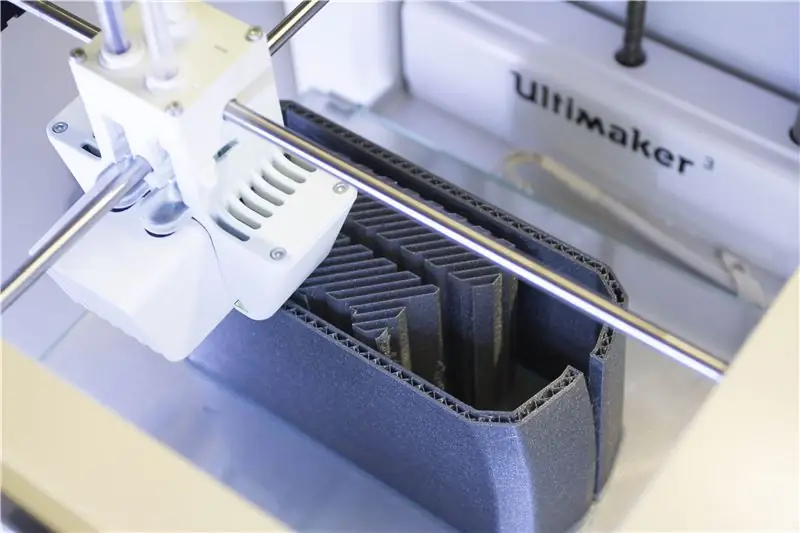
En af de vigtigste designbeslutninger, jeg tog, var at adskille kabinetterne, hvilket resulterede i et rent udseende og gjorde det fleksible dæk i stand til at fungere uden ekstra stivhed fra kabinetterne. Jeg ville formidle de funktionelle aspekter ved HP Multi Jet Fusion -teknologien, så jeg besluttede at FDM udskrive hoveddelen af kabinetterne, hvilket reducerede omkostningerne og brugte derefter HP -delene til at understøtte og fastgøre dem til dækket. Dette gav en interessant æstetik, samtidig med at den var meget funktionel.
De FDM -trykte kabinetter blev delt i to for at hjælpe med udskrivning, da støttemateriale kunne elimineres fra ydersiden. Splitlinjen blev omhyggeligt placeret for at sikre, at den blev skjult af HP -delen, når den blev spændt fast på brættet. Huller til motorforbindelserne blev tilføjet, og forgyldte kuglestik blev limet på plads til
Gevindindsatser blev indlejret i bambusdækket for at fastgøre kabinetterne til brættet og blev slebet i plan med brædderets overflade for at sikre, at der ikke var mellemrum mellem dækket og kabinettet.
Trin 4: Elektronik
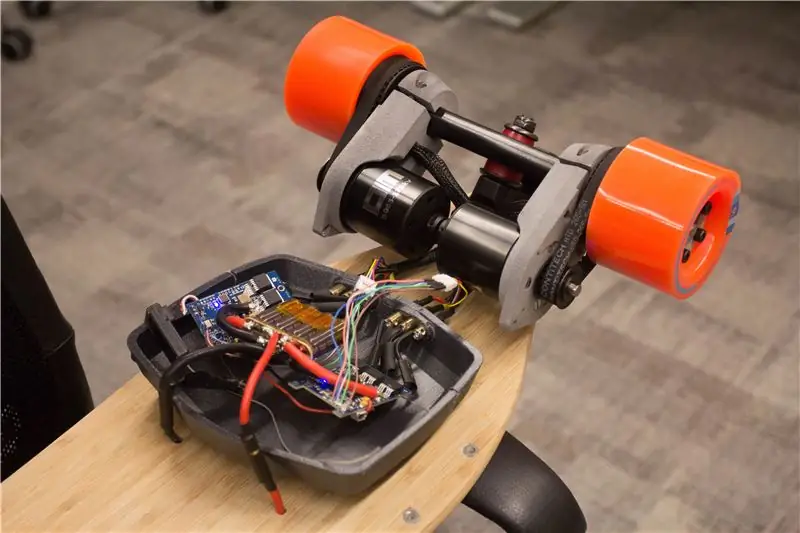
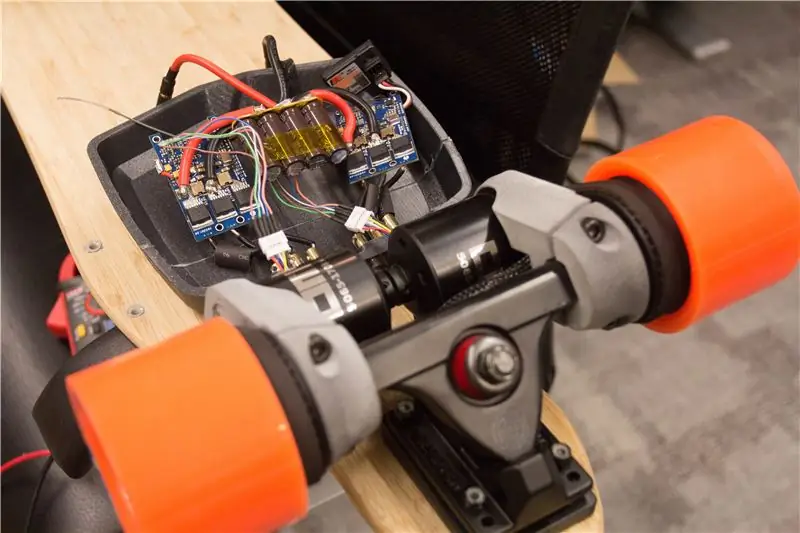
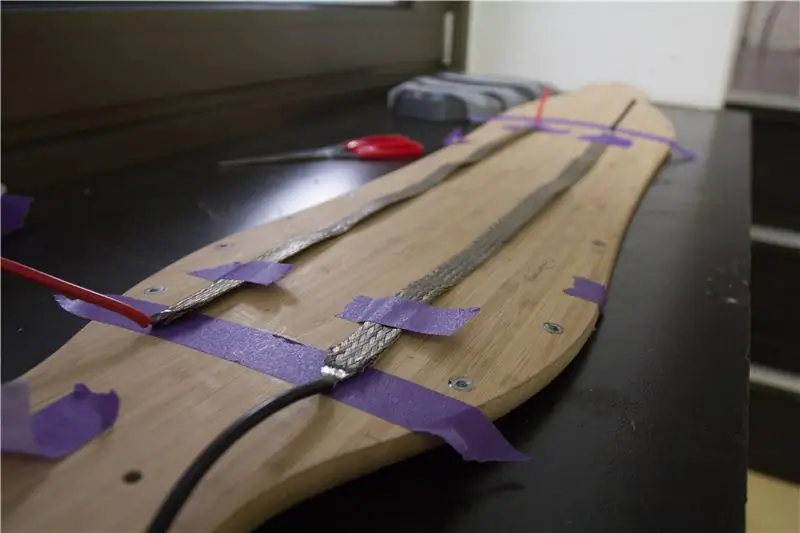
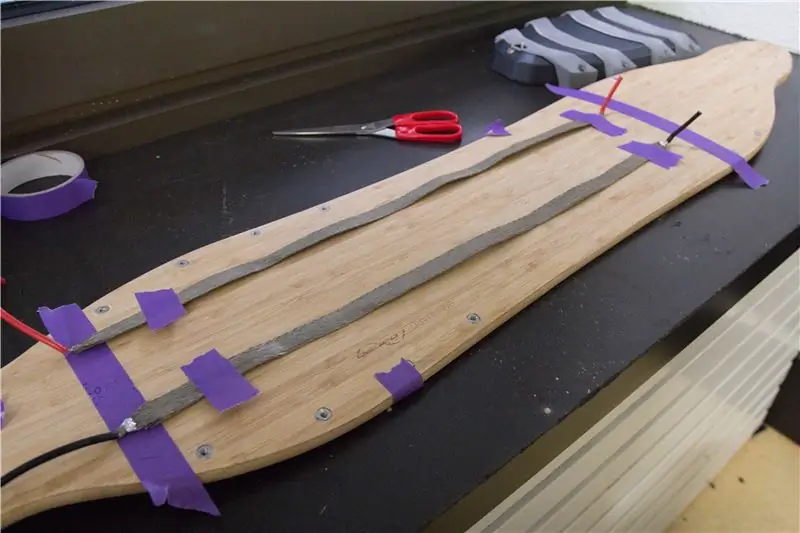
Elektronikken blev omhyggeligt valgt for at sikre, at tavlen var kraftfuld, men også intuitiv at bruge. Dette kort kan potentielt være farligt, hvis der skulle opstå fejl, så pålidelighed er en meget vigtig faktor.
Batteripakken består af 20 individuelle 18650 litiumionceller, der er punktsvejset sammen til en 42v pakning. 2 celler svejses parallelt og 10 i serie; cellerne jeg brugte var Sony VTC6. Jeg brugte en punktsvejser til at svejse nikkeltapperne til at danne pakken, da lodning skaber for meget varme, som kan beskadige cellen.
Strømmen fra batterikabinettet blev overført til hastighedsregulatorboksen ved hjælp af fladt flettet kabel, der blev kørt lige under grebbåndet på oversiden af dækket. Dette tillod kablerne at blive 'skjult' og eliminerede behovet for at føre kabler på undersiden, hvilket ville have set grimt ud.
Da dette er et dobbelt motorbræt, kræves to hastighedsregulatorer til uafhængigt at styre hver motor. Jeg brugte VESC hastighedsregulator til denne build, som er en controller specielt designet til elektriske skateboards, hvilket gør den meget pålidelig til denne brug.
De anvendte motorer er 170kv 5065 udløbere, der hver kan producere 2200W, hvilket er meget strøm til dette bord. Med den nuværende gearopsætning er bræddernes maksimale hastighed omkring 35MPH og accelererer meget hurtigt.
Den sidste fase var at oprette en fjernbetjening til at styre tavlen. Et trådløst system blev foretrukket på grund af den lettere betjening. Det var imidlertid vigtigt at sikre høj pålidelighed for transmission, da et fald i kommunikation kunne have alvorlige sikkerhedsproblemer, især ved høje hastigheder. Efter at have testet et par radiotransmissionsprotokoller besluttede jeg at 2,4 GHz radiofrekvens ville være den mest pålidelige for dette projekt. Jeg brugte en RC -bilsender på hylden, men reducerede størrelsen betydeligt ved at overføre elektronikken til en lille håndholdt kasse, der var 3D -printet.
Trin 5: Færdig bord og promoveringsvideo
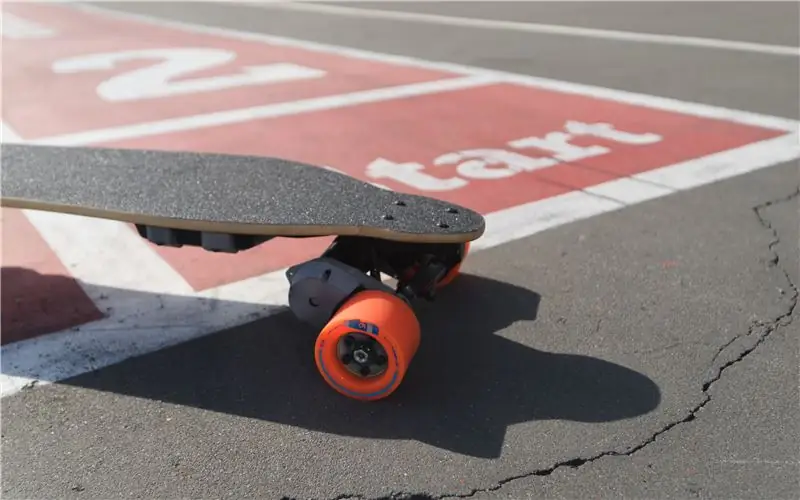
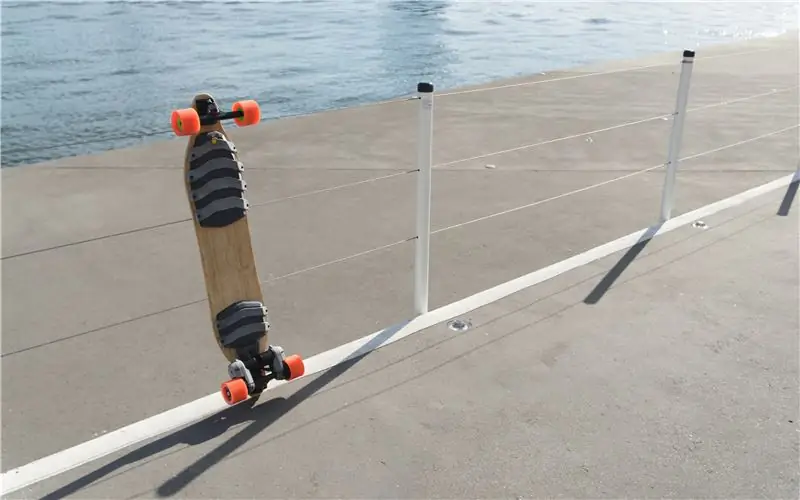
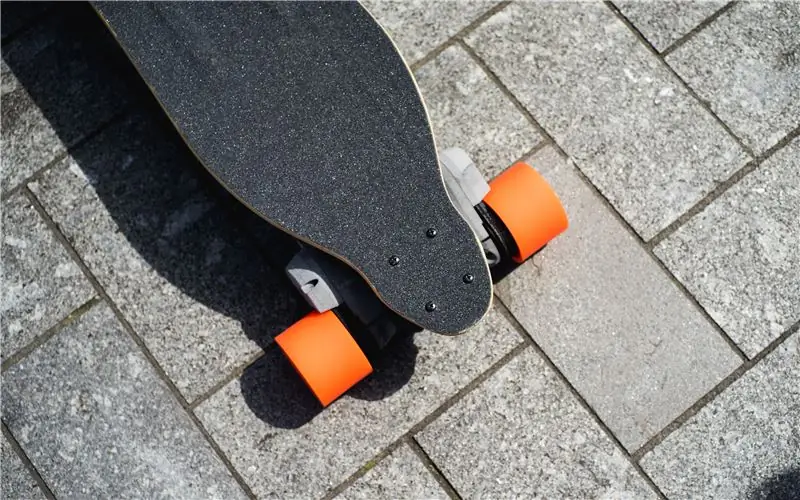
Projektet er nu færdigt! Vi har lavet en ret fantastisk video af brættet i aktion, du kan tjekke det herunder. Stor tak til 3D Hubs for at gøre det muligt for mig at udføre dette projekt - se dem her for alle dine 3D -udskrivningsbehov! 3dhubs.com
Anbefalede:
Styr kraftfuld elektrisk skateboard E-cykel 350W DC-motor ved hjælp af Arduino og BTS7960b: 9 trin
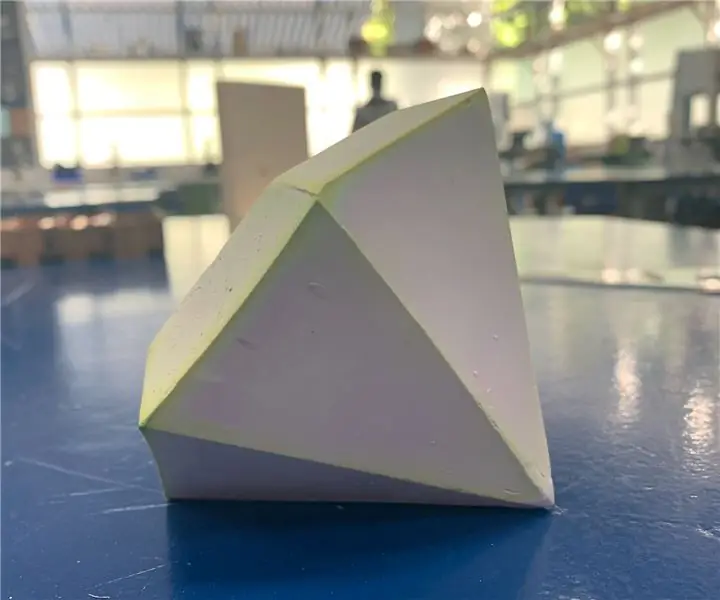
Kontrol Kraftfuld elektrisk skateboard E-Bike 350W DC-motor ved hjælp af Arduino og BTS7960b: I denne vejledning skal vi lære at styre en DC-motor ved hjælp af Arduino og Dc driver bts7960b. Motoren kan være en 350W eller bare en lille Toy arduino DC-motor så længe strømmen ikke overstiger BTS7960b driveren Max strøm. Se videoen
Speedboard: Elektrisk Skateboard: 5 trin
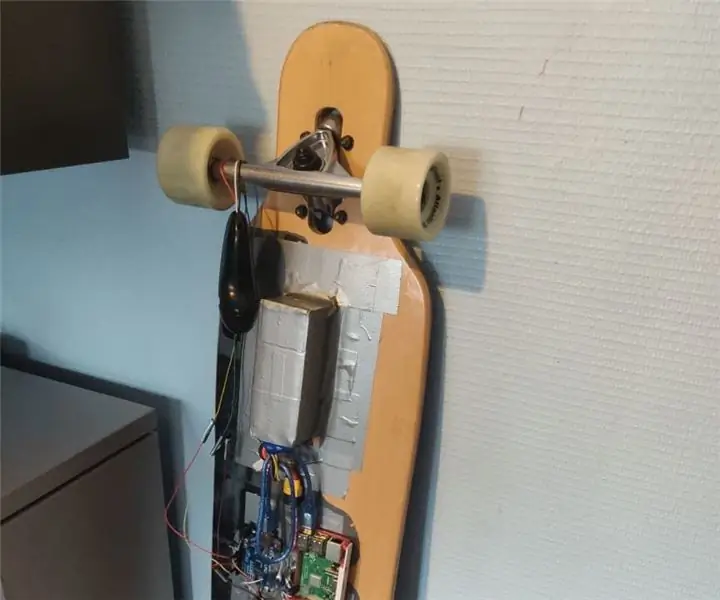
Speedboard: Elektrisk Skateboard: Hej! Jeg er en MCT College Student fra Howest i Belgien. I dag vil jeg give dig en trin for trin guide til, hvordan man laver et elektrisk skateboard med en hindbærpi og arduino. Jeg blev inspireret til at lave dette projekt af en berømt youtuber kaldet Casey Neistat
Fjernbetjening til elektrisk skateboard: 7 trin
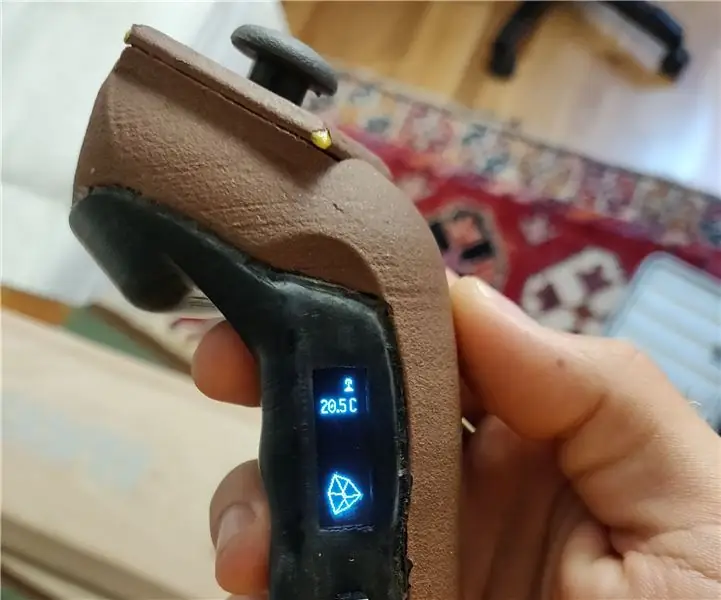
Fjernbetjening til elektrisk skateboard: Opret en fjernbetjening til elektrisk skateboard, i JAVASCRIPT! Deltag i min rejse, forhåbentlig lærer du noget. Dette vil ikke være en trinvis vejledning. Det vil mere være et udstillingsvindue, hvad jeg har brugt, hvordan jeg gjorde det, og jeg er sikker på, at du kan gøre det til. Jeg kan endda anbefale
Kilometertæller til elektrisk skateboard: 5 trin
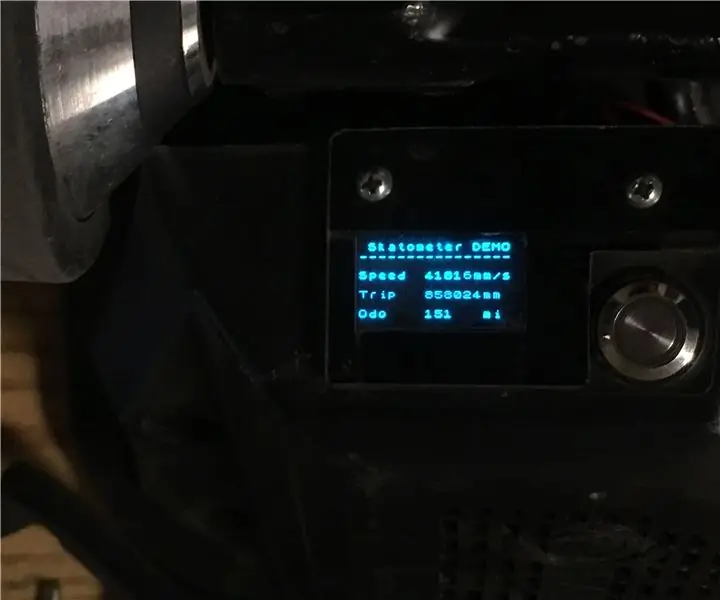
Elektrisk Skateboard kilometertæller: Introduktion De fleste avancerede elektriske skateboarder omkring tusinde dollars kommer med en telefonapp, der viser skateboard-oplysninger i realtid, og desværre følger de mere omkostningseffektive skateboards fra Kina ikke med dem. Så hvorfor ikke
DIY elektrisk skateboard: 14 trin (med billeder)
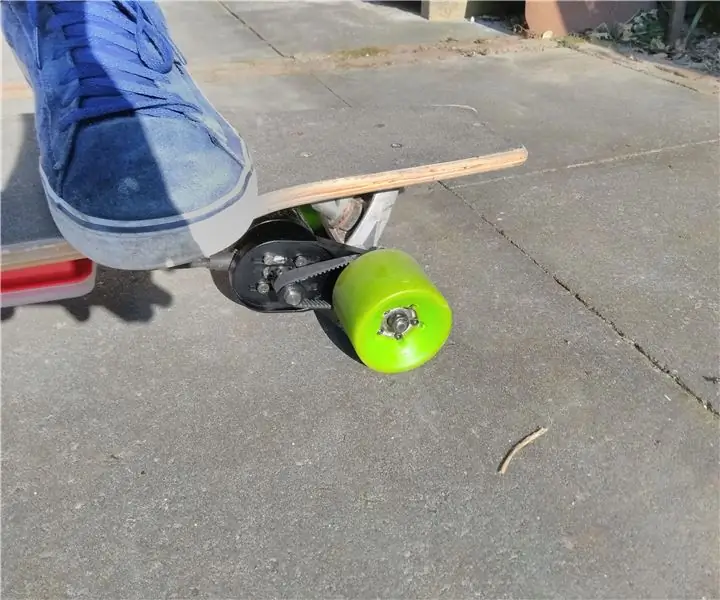
Diy Electric Skateboard: Efter 2 års forskning har jeg bygget mit første elektriske skateboard. Siden jeg har set en instruerbar, hvordan du bygger dit eget elektriske skateboard, har jeg været forelsket i DIY elektriske skateboards. At lave dit eget elektriske skateboard er en form for